Matter and Materials: Identify and apply knowledge of organic molecules in everyday life and industrial context
Unit 5: Plastics
Emma Harrage
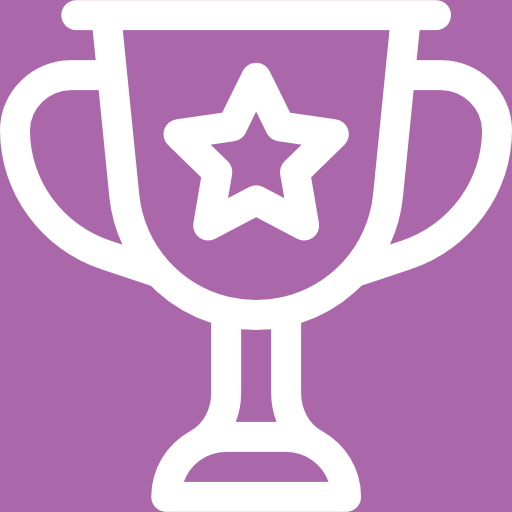
Unit outcomes
By the end of this unit you will be able to:
- Understand how plastics and polymers are made and refer to related South African industry.
- Understand the difference between thermoplastics and thermosets.
What you should know
Before you start this unit, make sure you can:
- Understand hydrocarbons. Refer to level 4 subject outcome 5.3 unit 1 if you need help with this.
Introduction
Parts of the text in this unit were sourced from Siyavula Physical Science Gr 12 Learner’s Book, Chapter 4, released under a CC-BY licence.
In this unit you will learn about plastics: how they are made, what they are used for and plastic pollution. Plastic is a very versatile material. It can be easily shaped, it is waterproof, and it can be coloured.
What is plastic?
Plastic is defined as a material that contains, as an essential ingredient, an organic substance of large molecular mass.
The word, plastic, was derived from the word ‘plastikos’ meaning ‘to mould’ in Greek. Hydrocarbons from fossil fuels act as building blocks for long polymer molecules which are used to make different types of plastics.
- Plastics are extremely useful because they are:
- strong and ductile
- poor conductors of heat and electricity
- easily moulded into different shapes and sizes
- resist corrosion
- resistant to many chemicals.
Many companies in South Africa manufacture plastic products including Sasol which is a worldwide supplier in multiple industries such as construction and infrastructure, packaging, household and consumer goods, plastics and polymers, agriculture, industrial products, textile, health and medical supplies.
However, as we learnt in level 2 subject outcome 7.1 unit 2, plastics are not biodegradable and the incorrect disposal of them can contribute to pollution.
Plastics and polymers
are large molecules (macromolecules) that are made up of many repeating structural units called which have various functional groups. To put it more simply, a monomer is like a building block.
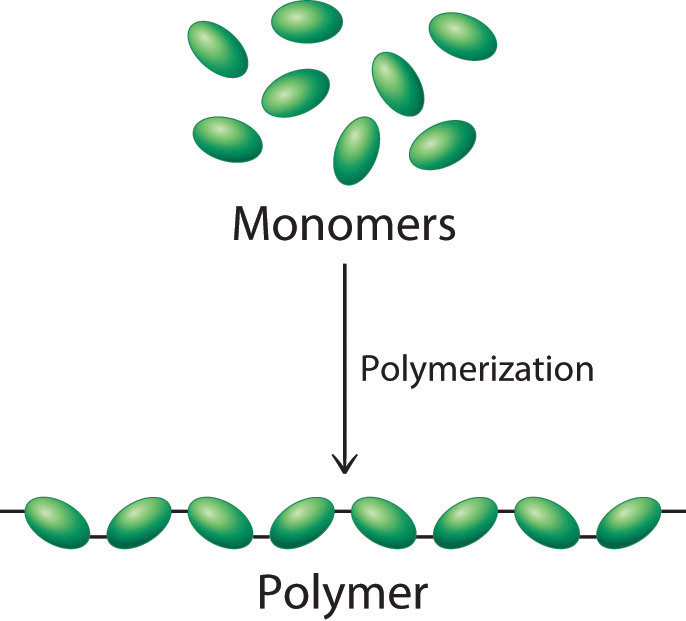
In an organic polymer, the monomers are joined by the carbon atoms of the polymer backbone or chain. A polymer can also be inorganic, in which case there may be atoms such as silicon in the place of carbon atoms. We will look solely at organic polymers.
Polymers are a specific group of . A macromolecule is any compound with many atoms.
The key feature that makes a polymer different from other macromolecules is the repetition of identical or similar monomers in the polymer chain. Polymers contain chains of the same type of functional group and that functional group is dependent on the monomer used.
Plastics are a group of polymers that can be moulded during manufacture. They can be one polymer or a blend (mixture) of polymers and may contain other substances as well. These other substances can be inorganic (e.g. used for electronic packaging) or stabilising (e.g. used for increasing fire resistance).
Depending on physical properties, plastics are divided into two types: thermoplastics and thermosetting plastics.
Polymers are formed through a process called , where monomers react together to form a polymer chain. Two of the types of polymerisation reactions are addition polymerisation and condensation polymerisation.
The formation of polythene from ethene is an example of polymerisation. Small ethene monomers join to each other by the breaking of the double bond allowing them to join up to form one long carbon chain of poly(ethene).
For example:
propene → poly(propene)
Where propene is a monomer and polypropene is a polymer.
Addition polymerisation: In this type of reaction, monomer molecules are added to a growing polymer chain one at a time.
Condensation polymerisation: In this type of reaction, two monomer molecules combine by means of a covalent bond, and a small molecule such as water is lost in the bonding process. Nearly all biological macromolecules are formed using this process. Polyesters are polymers that form through condensation polymerisation.
Thermoplastics
Thermoplastics can be melted down at high temperatures and can cool to gain back solid form, and are generally of high molecular mass. The polymer chains are held together via intermolecular forces. The intermolecular forces can be easily broken by adding sufficient energy. This explains why this polymer is mouldable and will melt upon heating. When enough energy is provided to overcome the intermolecular forces that hold the polymer together as a solid, the solid will melt. When it cools, it gives off heat and the intermolecular forces re-form, making it a solid. Therefore, the process is reversible.
Examples of thermoplastic materials are polyethylene, polypropylene, polyvinyl chloride, polystyrene, polyamides, polyesters, and polyurethanes.
- Acrylonitrile butadiene styrene (ABS) is a thermoplastic used to manufacture:
- sports equipment
- toys
- various automobile parts.
- Polycarbonate is used to make:
- CDs and DVDs
- drinking bottles
- food storage containers
- eyeglass lenses.
- Polyethylene is probably the most common thermoplastic and is used to make:
- shampoo bottles
- plastic grocery bags
- bullet-proof vests.
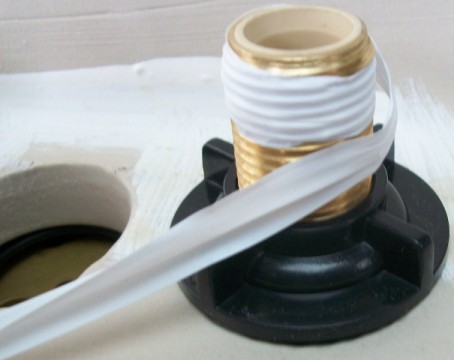
- The advantages of thermoplastics:
- the primary advantage of thermoplastics is its wide range of applications
- they are extremely adhesive to metal
- thermoplastics are lightweight materials
- they have high strength and have relatively low processing costs
- they are highly recyclable
- they have superb impact resistance and can be remoulded and reshaped
- they have excellent corrosion resistance and detergent and chemical resistance
- they provide electrical insulation.
- The disadvantages of thermoplastics:
- thermoplastics degrade easily in direct sunlight or under UV exposure
- not all thermoplastics resist hydrocarbons, organic solvents, and polar solvents
- they can fracture rather than deform under high stress.
Thermosetting plastics
Thermosets are types of plastics that can withstand high temperatures without melting. This toughens and/or hardens soft and viscous pre-polymers through the introduction of cross-links between polymer chains.
This process is known as ‘curing’ and it is done by heating the material above [latex]\scriptsize \displaystyle 200\text{ }{}^\circ \text{C}[/latex] and using additives. The cross-links are stable chemical bonds. Once the polymer is cross-linked, it becomes a very rigid and strong 3-D structure and will not melt upon heating.
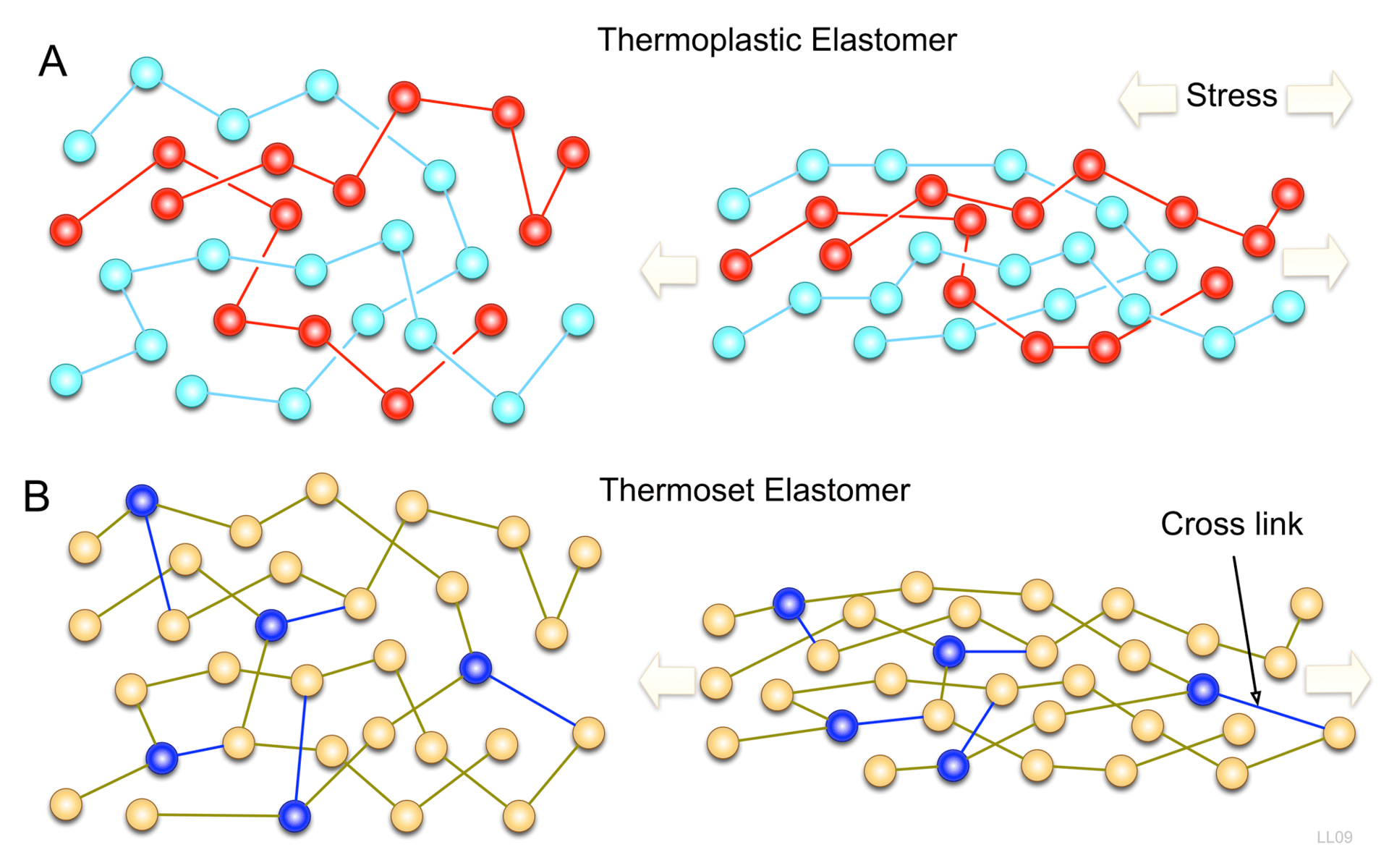
During the process of cross-linking, the molecular mass of the polymer increases; hence the melting point increases. When we heat up thermosets to uncontrollably high temperatures, they decompose instead of melting due to reaching the decomposition point before the melting point.
Thermosetting plastics are generally stronger than thermoplastic materials due to the cross-linking and are also better suited to high-temperature usage because they keep their shape as the strong covalent bonds between polymer chains cannot be broken easily.
These are some of the common uses of thermosetting polymers:
- to make kettles, plugs, laptop chargers, as they are heat resistant
- they are used in electrical fittings, handles and control knobs, and adhesives
- thermoset components are used extensively in a wide range of industries and are used for applications in the automotive, appliance, electrical, lighting, and energy markets due to excellent chemical and thermal stability along with superior strength, hardness, and moldability
- they are used to produce construction equipment panels
- they are used in agricultural equipment including feeding troughs and motors.
Some common examples of thermosets include polyester, fibreglass, polyurethanes, vulcanised rubber, acrylonitrile butadiene styrene (ABS), and melamine.
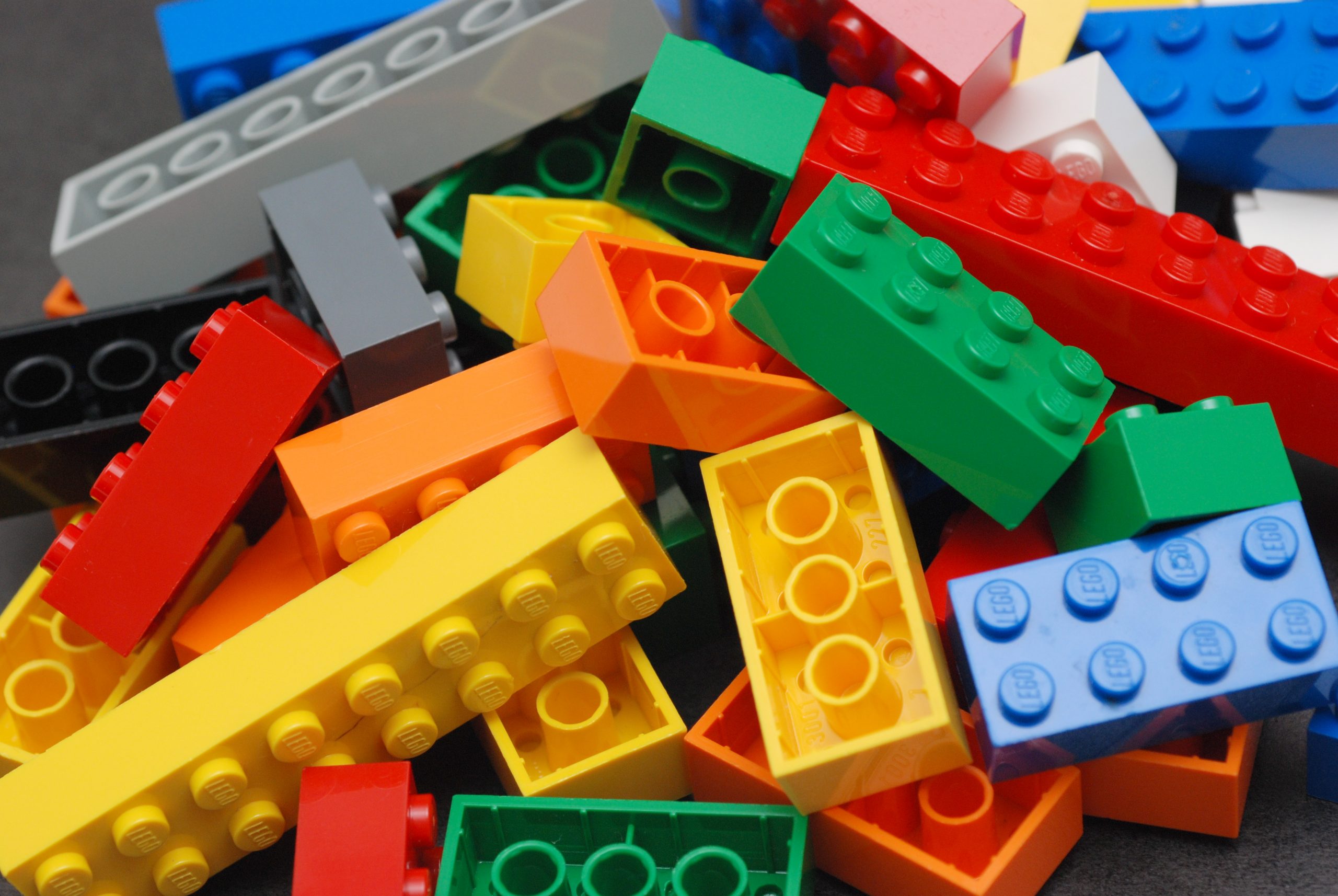
- The advantages of thermosetting plastics and their benefits over their metal counterparts:
- the choice of colour and surface finishes
- their resistance to corrosion effects and water
- their low thermal conductivity and microwave transparency
- their high strength-to-weight ratio and performance
- they are cost-effective
- their reduced production costs over fabrication using metals.
- There are certain disadvantages of thermosetting plastics :
- they cannot be recycled
- their low tensile strength and ductility
- they cannot be remoulded or reshaped
- their poor thermal conductivity when used for housing replacements
- they are much more difficult to surface finish
- the rigidity of the material can result in product failure when used in high vibration applications.
The difference between thermoplastic and thermoset plastic
The primary difference between the two is that thermoset is a material that strengthens when heated but cannot be remoulded or heated after the initial forming, while thermoplastics can be reheated, remoulded, and cooled as necessary without causing any chemical changes.
Thermoplastic | Thermoset plastic |
can be synthesised by the process called addition polymerisation | is synthesised by condensation polymerisation |
processed by injection moulding, extrusion process, blow moulding, thermoforming process, and rotational moulding | is processed by compression moulding, and reaction injection moulding |
has secondary bonds between molecular chains | has primary bonds between molecular chains and is held together by strong cross-links |
has a low melting point and low tensile strength | has a high melting point and tensile strength |
has lower molecular mass, compared to thermosetting plastic | has a high molecular mass |
Note
To consolidate your understanding of thermoset and thermoplastics, you can watch an edited version of this video, Fantastic Plastics. Or you can watch the full video on YouTube.
Types of plastics
There are various types of plastic that are commonly used for many day-to-day applications.
Polyethylene
When lots of ethene molecules bond together, a polymer called polyethene (commonly called polyethylene) is formed. Ethene is the unsaturated monomer which, when joined to other ethene molecules through an addition reaction, forms the saturated polymer polyethene. Polyethene is the most common plastic with over [latex]\scriptsize \displaystyle 80[/latex] million metric tons produced each year. It is cheap and is used to make squeeze bottles, plastic bags, films, toys, and moulded objects as well as electric insulation.
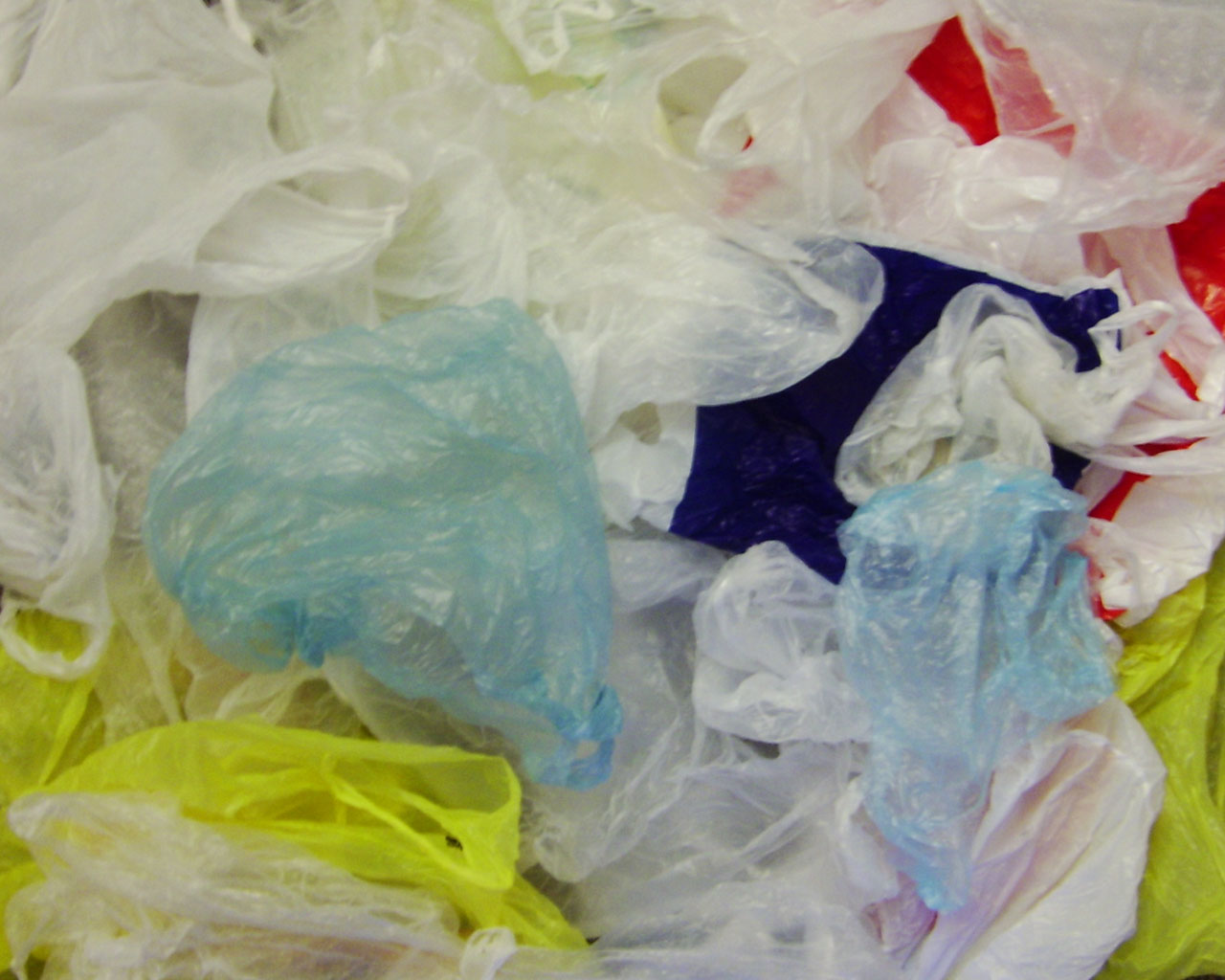
Polypropene (polypropylene)
Polypropene (commonly known as polypropylene) is stronger than polyethene and is used to make crates, fibres and ropes as well as being used in textiles, stationery, and car parts. In this polymer, the monomer is the alkene called propene.
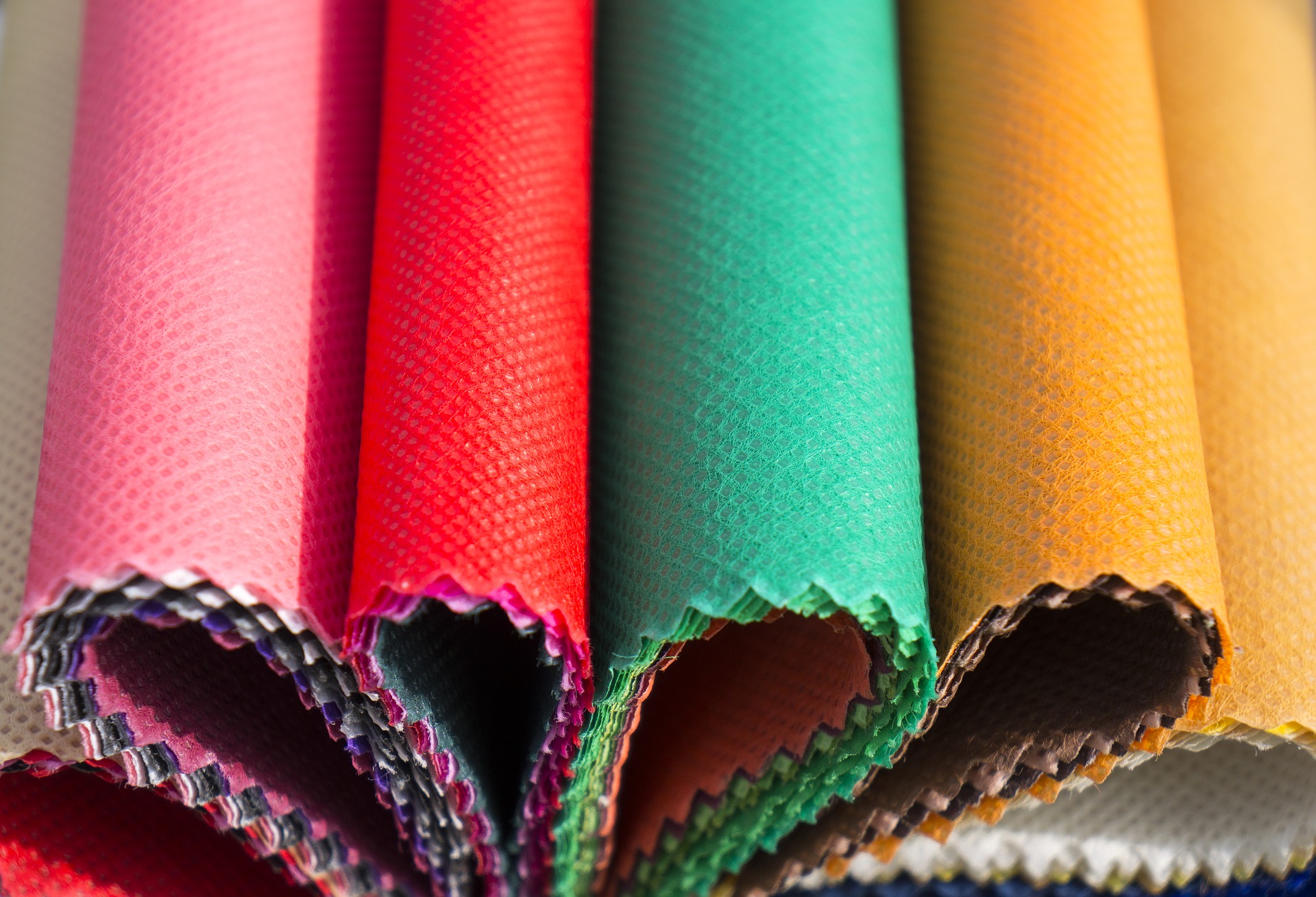
Polyvinyl chloride (PVC)
Polyvinyl chloride or PVC is formed from the monomer chloroethene, which is commonly known as vinyl chloride. PVC is used in construction, especially to make plastic piping. With the addition of a plasticiser it is also used in clothing and upholstery and to replace rubber. The role of the plasticiser is to increase the ability of a material to change shape without breaking.
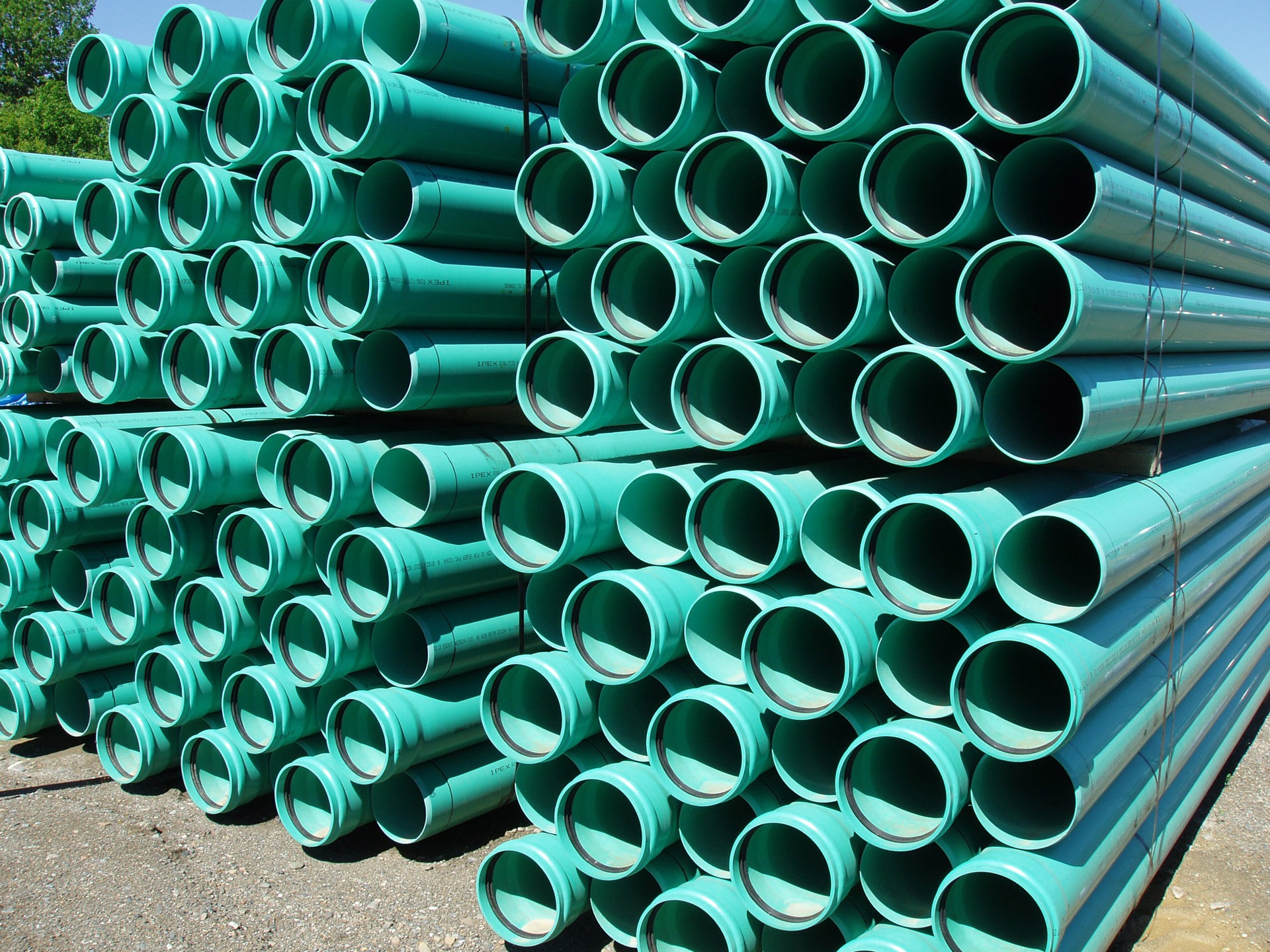
Polystyrene
Polystyrene is made from the monomer styrene which is a liquid petrochemical. Polystyrene has many uses including protective packaging, trays, plastic lids and bottles.
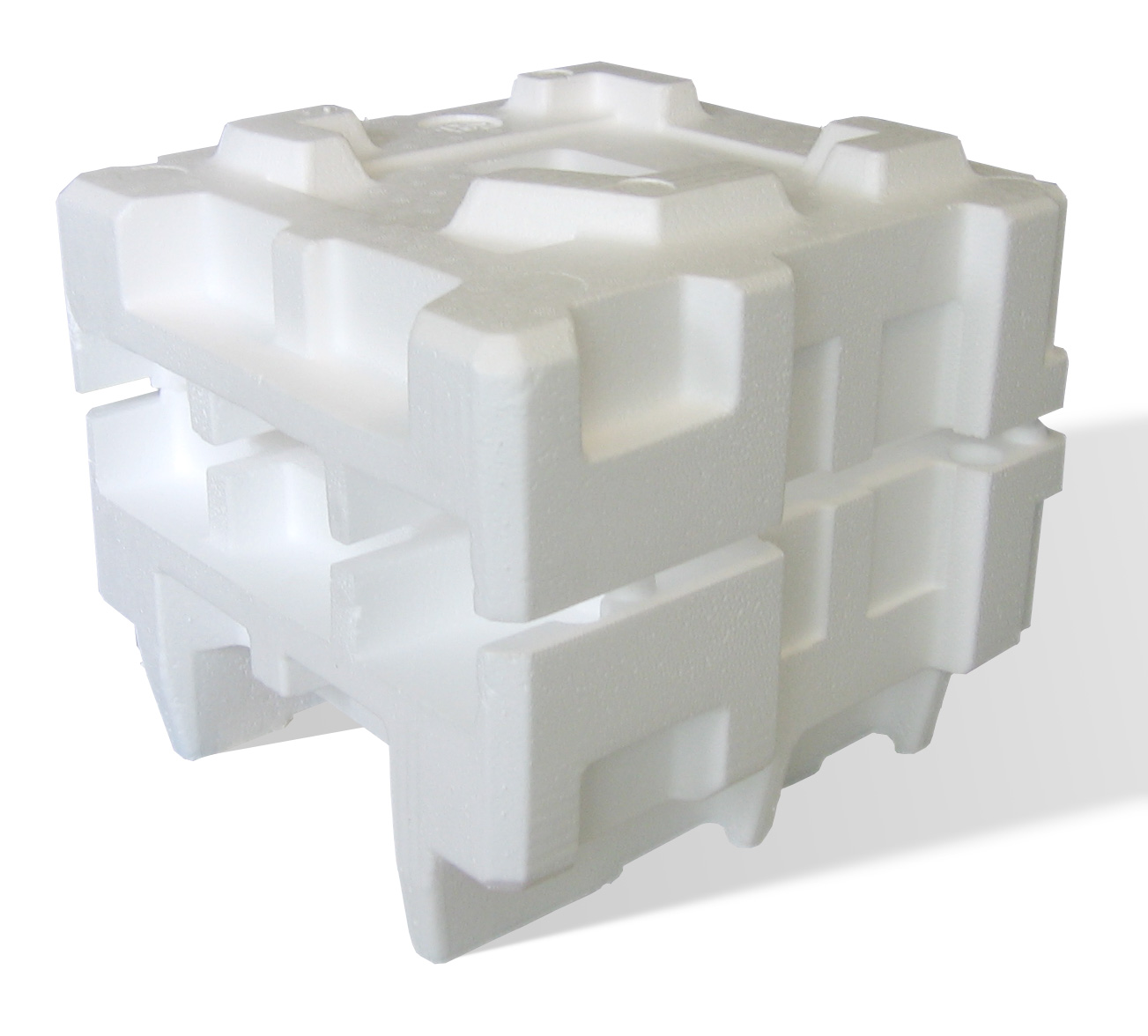
Polyethylene terephthalate (PET)
Although there are many forms of polyesters, the term polyester usually refers to polyethylene terephthalate (PET). PET is made from an alcohol and an acid.
Polyesters have several characteristics which make them very useful. They are resistant to stretching and shrinking, they are easily washed and dry quickly, and they are resistant to mildew. It is for these reasons that polyesters are being used more and more in textiles. Polyesters are stretched out into fibres and can then be made into fabric and articles of clothing. In the home, polyesters are used to make clothing, carpets, curtains, sheets, pillows, and upholstery.
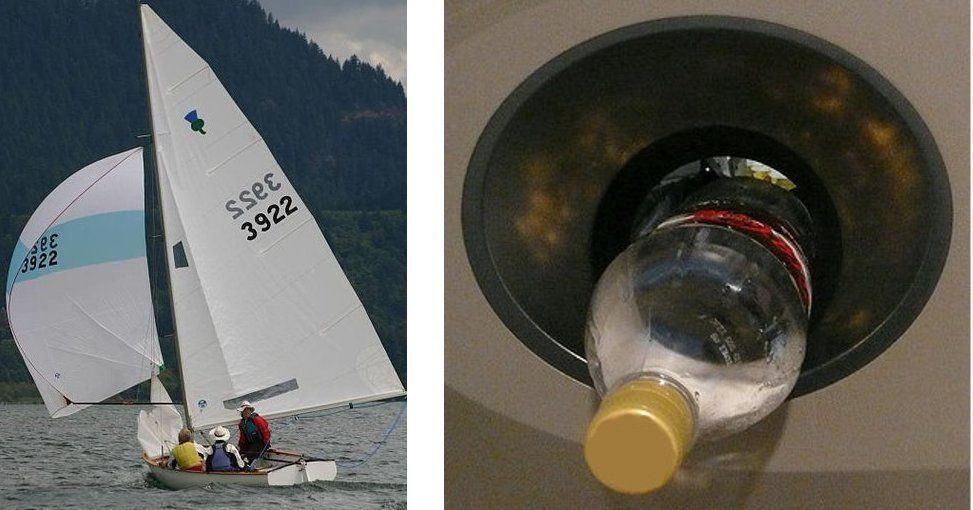
Polyethylene terephthalate (PET) is not just a textile, it is also used to make plastic drink bottles. Many drink bottles are recycled by being reheated and turned into polyester fibres. This type of recycling helps to reduce disposal problems.
Acrylonitrile butadiene styrene (ABS)
Acrylonitrile butadiene styrene (ABS) is made from the polymerisation and emulsion of acrylonitrile, butadiene, and styrene. It has the following properties that make it ideal for industrial environments because it is resistant to corrosion:
- a high degree of rigidity
- good impact resistance at a wide range of temperatures
- good insulation, weldability, and strain restraint
- a high degree of stability and strength.
Most importantly, ABS polymers are chemically nonreactive, making them resistant to acids, alkalis, alcohols, and oils.
ABS thermoplastics are also a great substitute for metals in automotive manufacturing to reduce weight. Commonly used plastic car parts include dashboard components, seat backs, seat belt parts, door loners, handles, instrument panels and pillar trims.
Other common uses of ABS plastics include:
- home appliances and consumer goods such as control panels, housings for vacuum cleaners, food processors, refrigerator liners
- electrical and electronic applications such as computer keyboards and electronic enclosures
- construction applications such as pipes and fittings; this is because of it has high impact strength, and good resistance to rust and corrosion
- musical instruments
- sports equipment
- gardening tools
- Lego blocks and other plastic toys
- medical applications such as nebulisers.
Polylactic acid (PLA)
Despite the name, polylactic acid (PLA) is a polyester. It is an interesting polymer because the monomer used for this polymer comes from the biological fermentation of plant materials, while most monomers used in plastics come from petroleum. As a result PLA is biodegradable and has low carbon dioxide emissions. PLA is mostly used for packaging material and because it is biodegradable, it has the potential to alleviate land-fill disposal problems.
Plastics and the environment
Although plastics have had a huge impact globally, there is also an environmental price that must be paid for their use. The following are just some of the ways in which plastics can cause damage to the environment.
- Waste disposal. Plastics are not easily broken down by micro-organisms and therefore most are not easily biodegradable. This leads to waste disposal problems.
- Air pollution. When plastics burn, they can produce toxic gases such as carbon monoxide, hydrogen cyanide and hydrogen chloride. When polystyrene is burnt carbon monoxide is released. When PVC is burnt, hydrogen chloride and carbon monoxide are released.
- Recycling. It is difficult to recycle plastics because each type of plastic has different properties and so different recycling methods may be needed for each plastic. Some plastics can be remelted and re-used, while others can be ground up and used as a filler. One of the problems with recycling plastics is that they must be sorted according to plastic type.
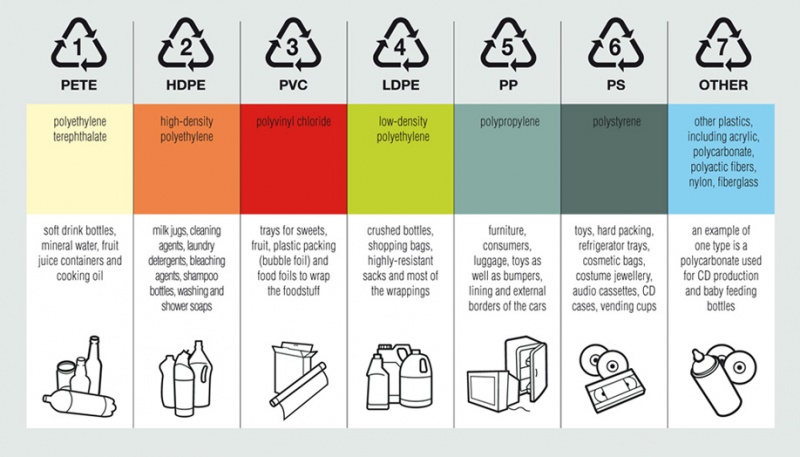
In many countries, including South Africa, shoppers must now pay for plastic bags. This encourages people to collect and re-use the bags they already have.
Summary
In this unit you have learnt the following:
- A polymer is a macromolecule that is made up of many repeating structural units called monomers, which are joined by covalent bonds.
- Polymers that contain carbon atoms in the main chain are called organic polymers.
- Polymers form through a process called polymerisation. Two examples of polymerisation reactions are addition reactions and condensation reactions.
- An addition polymerisation reaction occurs when unsaturated monomers (e.g. alkenes) are added to each other one by one. The breaking of a double bond between carbon atoms in the monomer means that a bond can form with the next monomer.
- Thermoplastic is a plastic polymer material that becomes pliable or mouldable at a certain elevated temperature and solidifies upon cooling.
- Thermosetting plastic is a polymer that irreversibly becomes rigid when heated.
- Polyethene, polypropene, polyvinyl chloride, polyvinyl acetate and polystyrene are all polymers formed through addition polymerisation.
- Polyethylene terephthalate and polylactic acid are polymers formed through condensation polymerisation.
- Plastics are a subgroup of organic polymers that can be moulded. They can contain more than one polymer.
- It is not easy to recycle all plastics and so they create environmental problems.
- Some of these environmental problems include issues of waste disposal, air pollution and recycling.
- Polylactic acid is an example of a biodegradable polymer made from renewable resources.
Unit 5: Assessment
Suggested time to complete: 15 minutes
For questions 1-9, answer by giving the letter of the correct answer only.
- What is the name of the small individual units that can be used to make plastics?
- Alkanes
- Polymers
- Monomers
- What is the main difference between thermoset and thermoplastic?
- They can both be recycled.
- Thermoset plastic cannot be heated and remoulded.
- Thermoplastic cannot be heated and remoulded.
- Which type of reaction occurs when plastics are made?
- Fractional distillation
- Cracking
- Polymerisation
- What does biodegradable mean?
- Something which is disposed of by burning.
- Can be broken down by bacteria in the soil and rots away.
- Something which can be easily reshaped.
- What type of plastic is used in electrical plugs and sockets?
- Biodegradable plastic
- Thermoplastic
- Thermoset plastics
- Which type of material would be best suited for a purpose where low weight, low density and high strength and heat resistance are important?
- Alloys
- Ceramics
- Plastics
- What is the monomer used to make polythene?
- Ethane
- Ethene
- Polythene
- What is the polymer made from styrene?
- Poly(ethene)
- Poly(styrene)
- Poly(styrane)
- Which of these toxic gases can be released by burning polyvinyl chloride?
- Hydrogen chloride (HCl)
- Carbon monoxide (CO)
- Hydrogen cyanide (HCN)
- What is the main difference between thermoplastic and thermosetting plastic?
- What is the main difference between the reactants used in an addition polymerisation and those used in a condensation polymerisation?
The full solutions are at the end of the unit.
Unit 5: Solutions
Unit 5: Assessment
- c
- b
- c
- b
- c
- c
- b
- b
- c
- The primary difference between the two is that thermoset is a material that strengthens when heated but cannot be remoulded or heated after the initial forming, while thermoplastics can be reheated, remoulded, and cooled as necessary without causing any chemical changes.
- A condensation reaction requires two different monomer molecules, and an addition reaction requires only one kind of monomer.
Media Attributions
- Fig 1 © Libre text is licensed under a CC BY-NC-SA (Attribution NonCommercial ShareAlike) license
- Fig 2 © Tomwsulcer is licensed under a Public Domain license
- Fig 3 © LaurensvanLieshout is licensed under a CC BY-SA (Attribution ShareAlike) license
- Fig 4 © Alan Chia is licensed under a CC BY-SA (Attribution ShareAlike) license
- Fig 5 © Trosmisiek is licensed under a Public Domain license
- Fig 6 © Anh Nhi Đỗ Lê - is licensed under a CC0 (Creative Commons Zero) license
- Fig 7 © Pixabay is licensed under a Public Domain license
- Fig 8 © Dubaj~commonswiki is licensed under a CC BY-SA (Attribution ShareAlike) license
- Fig 9 © Siyavula is licensed under a CC BY-NC (Attribution NonCommercial) license
- Fig 10 © igem is licensed under a CC0 (Creative Commons Zero) license
a large molecule consisting of monomers connected by covalent chemical bonds
a small molecule that can be combined through a reaction to form a polymer; it is a repeating unit in the polymer
any molecule containing many atoms
the process of bonding monomers, or single units together, to form longer chains called polymers