Chemical Systems and Industry: Identify and critically evaluate the impact of scientific knowledge on the chemical industries and the quality of human, environmental and socio-economic
Unit 1: Impact of Scientific Knowledge on Industry
Emma Harrage
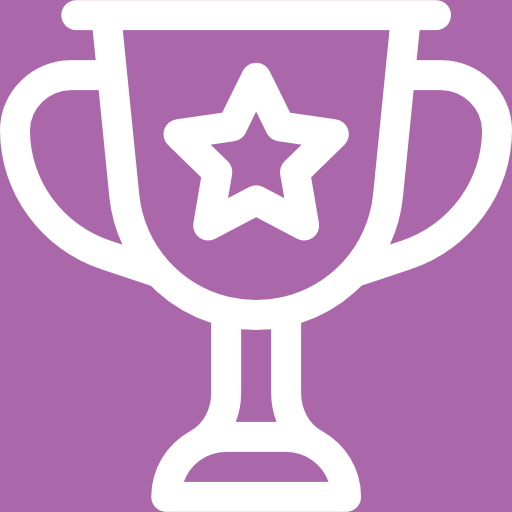
Unit outcomes
By the end of this unit you will be able to evaluate and identify the impact of scientific knowledge on certain industries in South Africa including:
- Organic chemistry: petroleum industry, paint, and adhesive manufacture.
- The production of soaps, cement, mining, the manufacture of explosives and fertiliser.
- Electrochemical and battery industries.
What you should know
Before you start this unit, make sure you can:
- Understand organic chemistry. Refer to level 4 subject outcome 5.2 units 1 if you need help with this.
- Understand redox reactions. Refer to level 4 subject outcome 6.2 unit 1 if you need help with this.
- Understand acids and alkalis. Refer to level 4 subject outcome 6.1 unit 1 if you need help with this.
- Understand chemical equilibrium. Refer to level 4 subject outcome 6.3 unit 1 if you need help with this.
Introduction
South Africa has developed an established, diversified manufacturing base which provides employment and economic empowerment.
Manufacturing in South Africa
Manufacturing in South Africa is dominated by the following industries:
Agri processing: Agriculture contributes [latex]\scriptsize \displaystyle 4\%[/latex] to South Africa’s gross domestic product (GDP) and consists of cattle and sheep farming, with only [latex]\scriptsize \displaystyle 13\%[/latex] of land used for growing crops. Maize is most widely grown followed by wheat, oats, sugar cane and sunflowers. Citrus and deciduous fruits are exported, as are locally produced wine and flowers.
Automotive: The automotive industry is one of South Africa’s most important sectors, with many of the major multinationals using South Africa to source components and assemble vehicles for both the local and international markets.
Chemicals: The synthetic coal and natural gas-based liquid fuels and petrochemicals industry is prominent, with South Africa being a world leader in coal-based synthesis and gas-to-liquids (GTL) technologies. South Africa’s chemical industry is of substantial economic significance to the country, contributing around [latex]\scriptsize \displaystyle 5\%[/latex] to the gross domestic product (GDP) and approximately [latex]\scriptsize \displaystyle 25\%[/latex] of its manufacturing sales. Sasol (through Sasol Chemical Industries and Sasol Polymers) is the most dominant, followed by AECI and Dow Sentrachem.
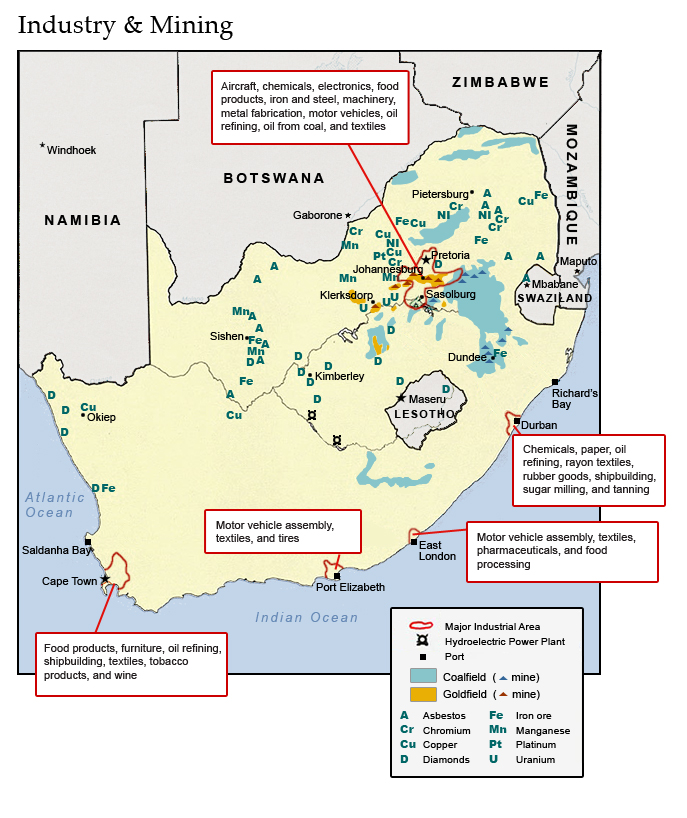
ICT and electronics: South African software developers are recognised as world leaders in innovation, production and cost efficiency backed by an excellent local infrastructure. This sector can be divided into three main sub-sectors: telecommunications, electronics, and information technology.
Metals: South Africa’s large, well-developed metals industry, with vast natural resources and a supportive infrastructure, represents a third of all South Africa’s manufacturing. It comprises basic iron ore and steel, basic non-ferrous metals, and metal products. The iron and steel basic industries involve the manufacture of primary iron and steel products from smelting to semi-finished stages.
Textiles, clothing, and footwear: Due to technological developments, local textile production has evolved into a capital-intensive industry, producing synthetic fibres in ever-increasing proportions.
The polyfins industry in South Africa
A polyfin is a type of polymer with the general formula[latex]\scriptsize \displaystyle {{\left( {\text{C}{{\text{H}}_{\text{2}}}\text{CHR}} \right)}_{\text{n}}}[/latex]. They are made from a handful of simple alkenes. Polyethylene and polypropylene are the most used commercially. More specialised polyfins include polybutene, polyisobutylene and polymethyl pentene.
Thermoplastic polyfins include the following:
- low-density polyethylene (LDPE)
- linear low-density polyethylene (LLDPE)
- very-low-density polyethylene (VLDPE)
- ultra-low-density polyethylene (ULDPE)
- medium-density polyethylene (MDPE)
- polypropylene (PP)
- polymethyl pentene (PMP)
- polybutene-1
- ethylene-octene copolymers
- stereo-block PP
- olefin block copolymers
- propylene–butane copolymers.
Polyolefin elastomers (POE) include the following:
- polyisobutylene (PIB),
- poly(a-olefin)s,
- ethylene propylene rubber (EPR),
- ethylene propylene diene monomer (M-class) rubber (EPDM rubber).
Polyfin properties range from liquidlike to rigid solids and are primarily determined by their molecular weight and degree of crystallinity. Polyfin surfaces have excellent chemical resistance and are unaffected by common solvents. They can be adhesively bonded and by some superglues. They are extremely inert chemically but show less strength at lower and higher temperatures.
The major applications for HDPE are film (wrapping of goods), blow moulding (e.g. liquid containers, such as bleach bottles), injection moulding (e.g., toys, screw caps), extrusion coating (e.g. coating on milk cartons), piping for distributing water and gas, insulation for telephone cables, wire and cable insulation.
LLPE is mainly (70%) used for film.
Major applications of polypropylene are injection moulding, fibres, and film. Compared to polyethylene, polypropylene is stiffer but less prone to breaking. It is less dense and more chemically resilient.
Petrochemical industry
South Africa’s fuel sector, including petrol, diesel, jet fuel, illuminating paraffin, fuel oil, bitumen, and liquefied petroleum gas, contributes about [latex]\scriptsize \displaystyle 8.5\%[/latex] to the country’s GDP while supplying about [latex]\scriptsize \displaystyle 18\%[/latex] of its primary energy. South Africa has six refineries, although three of them are currently shut and in need of investment. South Africa has a trade deficit in petrol and diesel, driven by demand from Eskom’s open cycle gas turbines, and demand from other sectors. South Africa is expected to become more dependent on fuel imports as the country’s six refineries face an uncertain future.
Two of the main companies involved in the petroleum industry are:
PetroSA: The Petroleum Oil and Gas Corporation of South Africa (SOC) Limited (PetroSA) is the national oil company of South Africa which is owned by the State and reports to the Department of Energy.
The core business activities of PetroSA are:
- The exploration and production of oil and natural gas.
- The production of synthetic fuels from offshore gas at one of the world’s largest Gas-to-
Liquid (GTL) refineries in Mossel Bay, South Africa.
- The development of domestic refining and liquid fuels logistical infrastructure.
- The marketing and trading of oil and petrochemicals.
PetroSA operates the FA-EM, South Coast gas fields as well as the Oribi and Oryx oil fields. These gas fields provide feedstock to the Mossel Bay GTL refinery. PetroSA’s GTL refinery produces synthetic fuels and products converted from natural methane-rich gas and condensate using a unique GTL Fischer-Tröpsch technology. Key commodities produced include unleaded petrol, kerosene (paraffin), diesel, propane, liquid oxygen and nitrogen, distillates, eco-fuels, and alcohols.
SASOL: Sasol Mining operates six coal mines that supply feedstock for Secunda (Sasol Synfuels) and Sasolburg (Sasolburg Operations) complexes in South Africa. While the coal supplied to Sasol Synfuels is used as gasification feedstock, some is used to generate electricity. The coal supplied to the Sasolburg Operations is used to generate electricity and steam.
Sasol operations include fuel blending and storage facilities at the Secunda operations to turn components into market ready products, such as:
- bitumen
- industrial heating fuels
- naphtha, and illuminating paraffin
- transport fuels, (petrol, diesel and jet fuels)
- lubricants and lubricant base oils
- liquefied petroleum gas (LPG)
- automotive lubricants
- industrial lubricants
- greases
- cleansers and degreasers
- automotive fuels
- burner fuels
Fischer-Tröpsch processes
The Fisher-Tröpsch process is used to create chemicals called alkanes. Sometimes the gas methane is produced, which is generally undesirable. Sometimes, different kinds of alcohols are produced in small amounts.
Sasol’s Fischer-Tröpsch hard waxes are synthetically produced by using gas-to-liquids (GTL) technology, in which Sasol is globally recognised as a commercial and technical pioneer. High-Temperature Fischer-Tröpsch (or HTFT) is performed at temperatures of [latex]\scriptsize \displaystyle \text{330 }\!\!{}^\circ\!\!\text{ C - 350 }\!\!{}^\circ\!\!\text{ C}[/latex]. HTFT uses an iron-based catalyst. Sasol uses HTFT in Coal-to-Liquid plants (CTL).
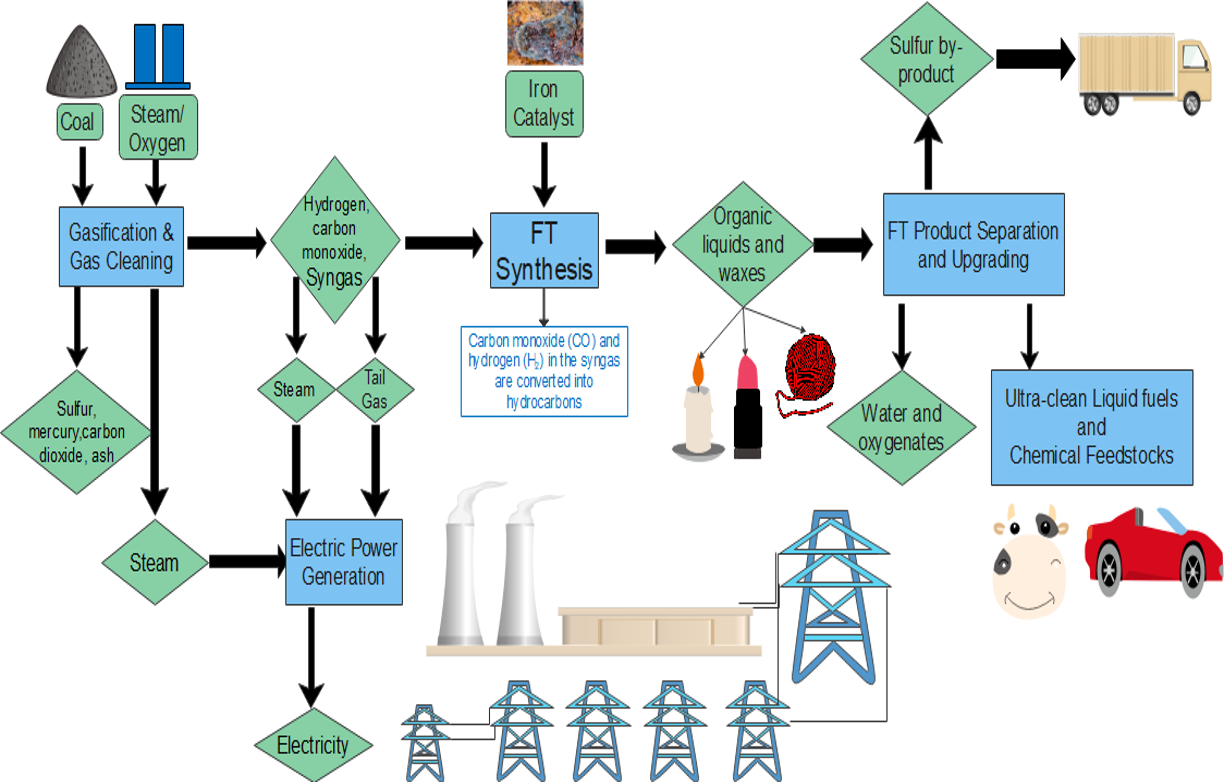
Many different catalysts can be used for the Fischer-Tröpsch process. The most common catalysts are the metals cobalt, iron, and ruthenium. Cobalt is the most active catalyst (it has the greatest and fastest effect on the process). When the input is a natural gas, cobalt catalysts are very good for the Fischer-Tröpsch process. Iron catalysts are better when the input gas is of lower quality (less pure) such as coal or biomass.
Most metals used for this process (such as cobalt, nickel, and ruthenium) remain in their metal form when added to the process. However, iron catalysts behave very differently. Often, iron catalysts change form and chemical phase, like converting into various oxides and carbides during the reaction. It is important to control all of the iron reactions during the process, or else the process may not work correctly.
The GTL process uses natural gas, to produce hard waxes. With the combination of high melting point, low viscosity, and excellent hardness even at high temperatures, hard waxes provide a useful variety of applications. The Sasol process turns natural gas into energy and chemical products, including transport fuels, base oils, waxes, paraffins and naphtha.
The liquid fuels produced are high-performance, low-emission products. The synthetic GTL-based diesel is an environmentally cleaner burning fuel as it leads to a reduction in carbon monoxide, hydrocarbon, and particulate matter without compromising NOx emissions even when compared to European sulfur-free diesel.
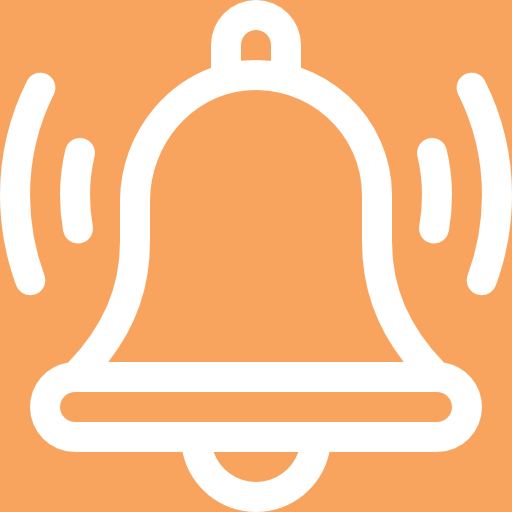
Take note!
Sasol was founded in 1950 by the state-owned Industrial Development Corporation to produce gasoline from hard coal based on the Fischer-Tröpsch synthesis. The technique of coal liquefaction was considered unprofitable at the time and was used because South Africa was subject to extensive sanctions during the apartheid era, which made it difficult to source crude oil, while domestic coal could be extracted cheaply. Production began in 1955.
The company owns plants in 17 countries on three continents, namely in Belgium, Brazil, the People’s Republic of China, Germany, Dubai, France, Italy, Japan, Netherlands, Poland, Russia, Singapore, Slovak Republic, Spain, South Africa, United States, and the United Kingdom.
Sasol’s primary business is the further processing of coal and natural gas by means of coal gasification and Fischer-Tröpsch synthesis into gasoline and raw materials for the chemical industry in the Sasol 1 (Sasolburg) and Sasol 2 and 3 plants (both in Secunda). The low-temperature syngas conversion process is operated based on an iron-based catalyst to produce hydrocarbon waxes and paraffins. The syngas (mixture of hydrogen and carbon monoxide) is also converted into methanol, butanol, and ammonia. Ammonia is then converted into nitric acid and ammonium-based fertilisers and explosives.
The process also produces water and oxygenated hydrocarbons ethylene and ethane, which are then purified and marketed. The ethane is further cracked to make additional ethylene which is then converted into polyethylene for the polymer business. Propylene from the Secunda and Sasolburg plants are also converted into products such as polypropylene, butanol, butyl acrylate and ethyl acrylate. The acrylates are used to make superabsorbent polymers which are used in nappies. Through proprietary technology 1-hexene, 1-octene and 1-pentene are recovered from the oil stream. International customers use these as co-monomers for making speciality grade polymers.
The South African energy cluster operates coal mining in South Africa (Sasol mining), trades in natural gas from Mozambique (Sasol gas), operates the CtL plant in Secunda (Sasol synfuels), an oil refinery and processing plant, as well as various sales activities including filling stations (Sasol oil).
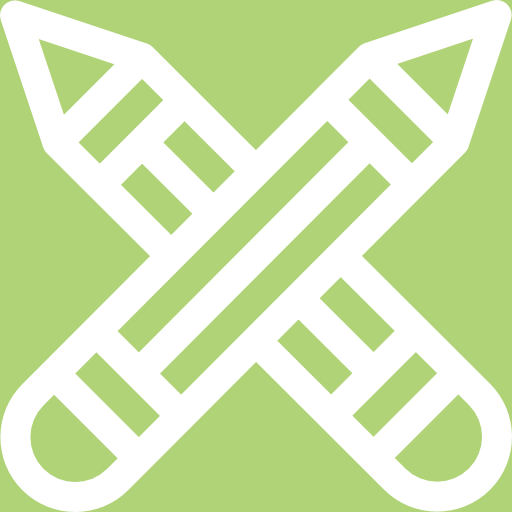
Exercise 1.1
- Using figure 2, answer the following questions:
- What is the first step in the process of turning coal into liquid fuels?
- Which catalyst is used in Sasol’s Fischer-Tröpsch process? Why is that one used?
- What happens to the heavy waxes produced in the Fischer-Tröpsch process?
- They are separated out
- They are mixed with gasoline
- They are subjected to cracking
- No heavy oil fractions are produced
The full solutions are at the end of the unit.
Paint and adhesives
South Africa has many manufacturers of paint and adhesives, including Plascon, Prominent Paints, Durham paints and Universal. Probably the most well-known adhesive manufacturer in South Africa is Pratley’s. Other major manufacturers include Alcolin, and Pattex.
Paint manufacture
The South African paint industry is valued at R11.5 billion per annum. The industry supports a value chain worth R150 billion, employs approximately 10 000 people and is an essential supplier to the construction and manufacturing sectors as many products cannot be sold without a protective coating.
A paint is composed of pigments, solvents, resins, and various additives. The pigments give the paint colour; solvents make it easier to apply; resins help it dry; and additives serve as everything from fillers to anti-fungicidal agents. The basic white pigment is titanium dioxide, selected for its excellent concealing properties, and black pigment is commonly made from carbon black. Other pigments used to make paint include iron oxide and cadmium sulfide for reds, metallic salts for yellows and oranges, and iron blue and chrome yellows for blues and greens.
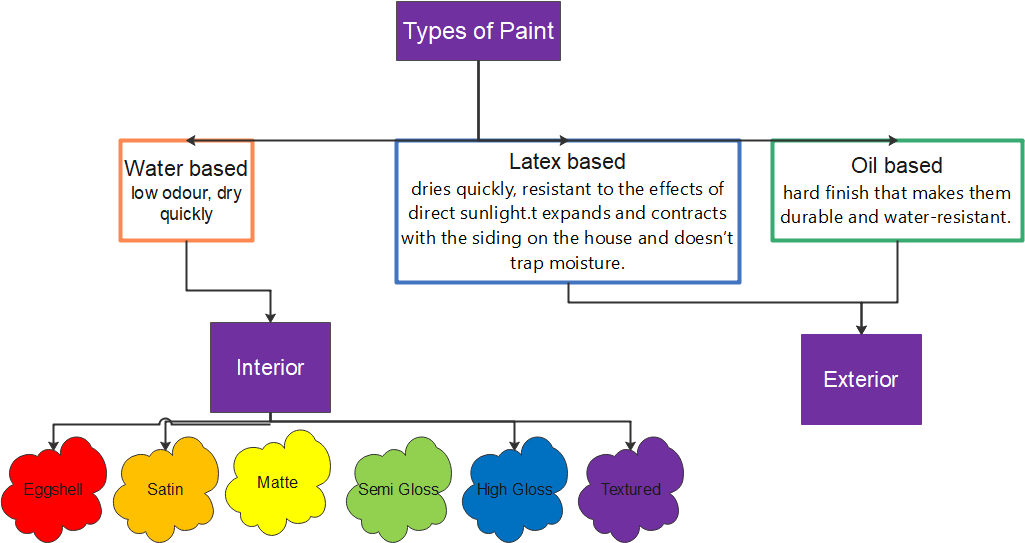
Solvents are various low viscosity, volatile liquids. They include petroleum mineral spirits and aromatic solvents such as benzol, alcohols, esters, ketones, and acetone. The natural resins most used are linseed, coconut, and soybean oil, while alkyds, acrylics, epoxies, and polyurethanes are among the most popular synthetic resins. Calcium carbonate and aluminium silicate are simply fillers that give the paint body and substance without changing its properties. Other additives produce certain desired characteristics in paint, such as the thixotropic agents that give paint its smooth texture, driers, anti-settling agents, anti-skinning agents, defoamers, and a host of others that enable paint to cover well and last long.
Adhesives
Adhesives, also known as glue, cement, mucilage, or paste, are any non-metallic substance applied to one or both surfaces of two separate items that binds them together and resists their separation.
The use of adhesives offers certain advantages over other binding techniques such as sewing, mechanical fastenings, or welding. These include the ability to bind different materials together, the more efficient distribution of stress across a joint, the cost-effectiveness of an easily mechanised process, and greater flexibility in design. Disadvantages of adhesive use include decreased stability at high temperatures, relative weakness in bonding large objects with a small bonding surface area, and greater difficulty in separating objects during testing.
Adhesives are typically organised by the method of adhesion followed by reactive or non-reactive, a term which refers to whether the adhesive chemically reacts to harden. Adhesives may be found naturally or produced synthetically.
There is hardly any product in our surroundings that does not contain at least one adhesive—be it the label on a beverage bottle, protective coatings on automobiles, or profiles on window frames. Market researchers forecasted a turnover of almost US [latex]\scriptsize \displaystyle 50[/latex] billion for the global adhesives market in [latex]\scriptsize \displaystyle 2019[/latex].
Adhesive type | Sources/properties | Common uses |
Animal glue | Obtained from animal by-products such as bones, blood, and hooves | Binding of abrasives in sandpaper and other grinding materials |
Casein | Main protein in milk | Labels on beer bottles that do not come off in ice water, yet are recyclable |
Starch | From corn and maize | Corrugated cardboard bonding |
Natural rubber | Not ‘sticky enough’ by itself but is used as an additive in other adhesives | Self-adhesive envelopes and other pressure-sensitive adhesives; adhesives that bond to substrates on contact (such as tapes) |
Butyl rubber/isobutylene | It is elastomeric – It stretches | Additive for hot-melt adhesives, window sealants, and pressure-sensitive adhesives |
Amino resins | Water-soluble adhesives | Bonding of layers in plywood and the bonding of particles in particle board |
Polyurethane | A flexible adhesive | Bonding soles to the bodies of shoes; also used in food packaging |
Polyvinyl acetate | Common ‘white’ glue | Book bindings and labels |
Polyolefin/ethylene copolymer | No solvents involved | Hot melts: these are thermoplastics applied in molten form (in the range) which solidify on cooling to form strong bonds between a wide range of materials; ethylene-vinyl acetate-based hot-melts are particularly popular for crafts because of their ease of use and the wide range of common materials they can join |
Acrylates or anaerobic adhesives | Cure when air is removed | Adhesive used to keep nuts tight on bolts, such as those within ATMs and heavy machinery |
Silicone | Both an adhesive and a sealant and the only common adhesive that is based on silicon rather than carbon | Bathtub and shower sealants; also many car applications, such as oil pans and head gaskets |
Note
The only South African product which has been to space is Pratley Putty. Pratley Putty is a clay-like adhesive dough designed by South African engineer George Montague Pratley from Krugersdorp. He discovered Pratley Putty in the 1960s while searching for a glue with which he could paste components into an electrical split box. Pratley Putty was used in 1969 to hold together parts of the Eagle moon landing craft of the Apollo 11 mission. It was the first to land on the moon. It is the only South African product to land on the moon.
Mining in South Africa
Minerals are natural compounds formed through geological processes. A mineral could be a pure element, but more often minerals are made up of many different elements combined. Minerals are useful chemical compounds for making new materials that we can use in our daily lives. Mining is an important industry in South Africa. We have a lot of mineral resources in our country and a lot of people depend on mining for a living.
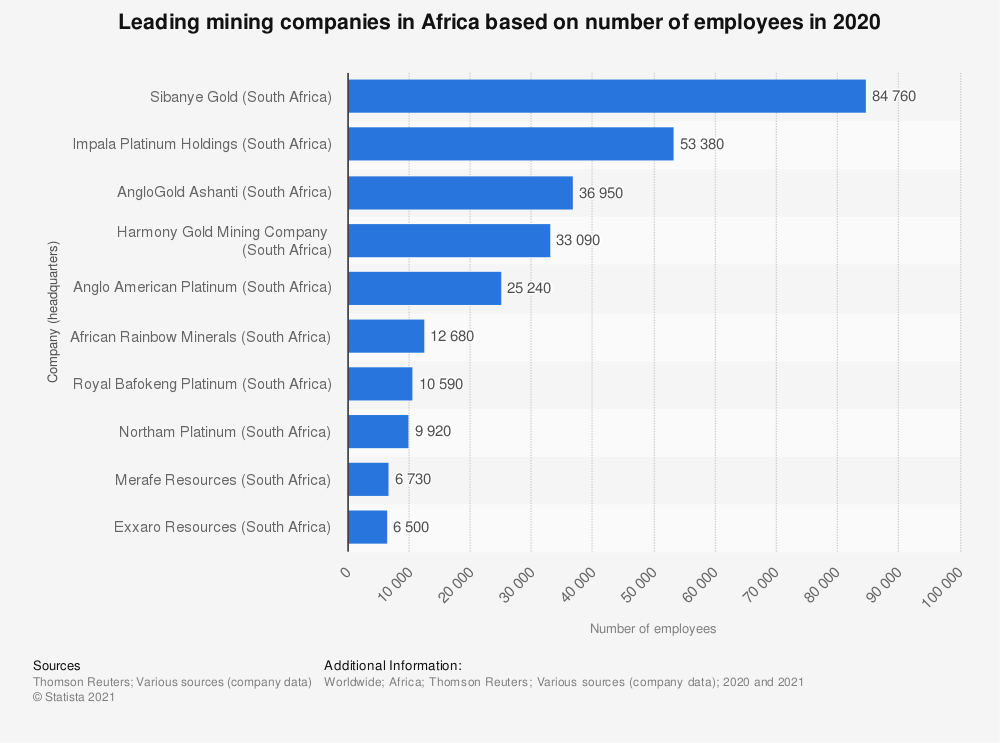
Long before diamonds were discovered in the Kimberley area and the Gold Rush in the Pilgrim’s Rest and Witwatersrand areas in the late 1800s, minerals have been mined in South Africa. At Mapungubwe in the Limpopo Province evidence of gold and iron mining and smelting was found which dates to the early 11th century AD. However, it was the large-scale mining activities that accelerated the development of the country.
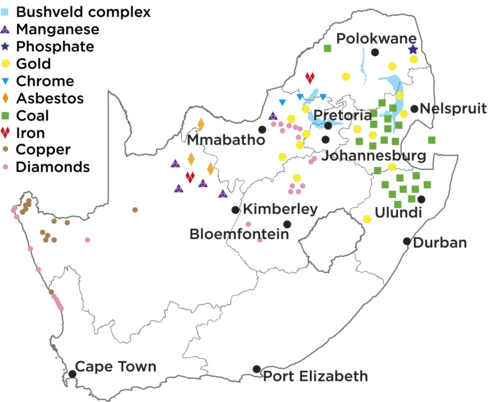
South Africa has a wealth of minerals. We are the world’s largest producers of chromium, manganese, platinum, vanadium and andalusite; and the second largest producer of ilmenite, palladium, rutile, and zirconium. We are the third largest coal exporter, fifth largest diamond producer and seventh largest iron ore producer. Up to 2010 we were the world’s largest gold producer, but our gold production has declined steadily over a number of years. We are currently fifth on the list of gold producers.
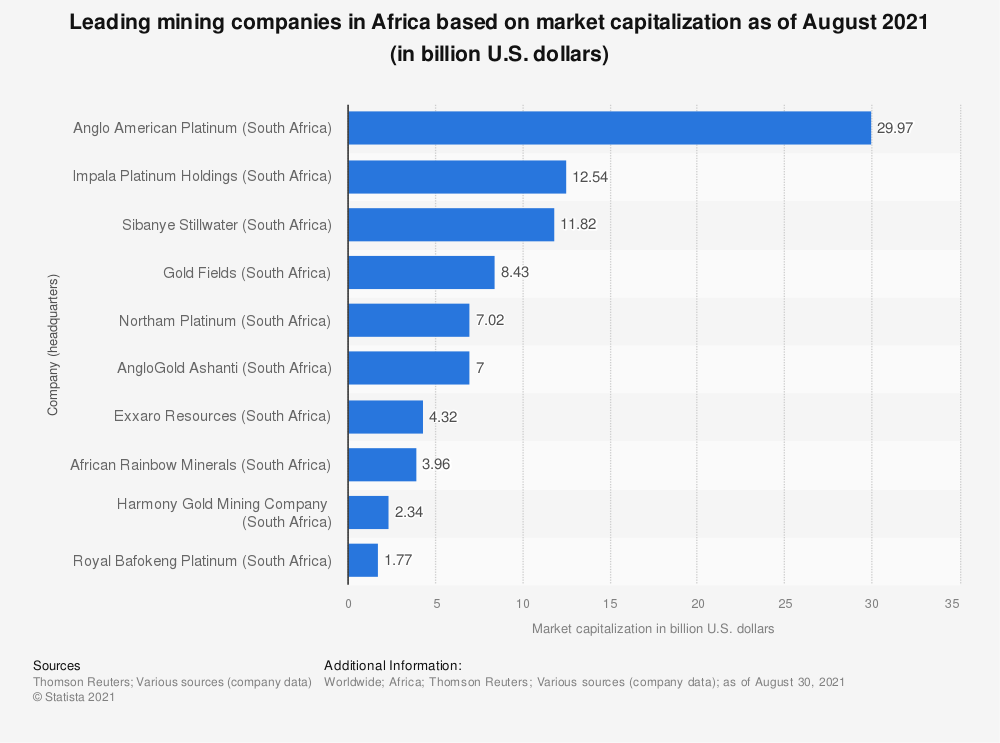
Mining has played a major role in the history of South Africa. It accelerated technological development and created infrastructure in remote areas in South Africa. Many small towns in South Africa started because of mining activity in the area. It also created a demand for roads and railways to be built. Most importantly it created job opportunities for thousands of people. Even today many households are dependent on the mining activities for jobs and an income. Mining is an important part of our economic wealth. We export minerals and ore to many other countries in the world.
- Extraction of iron: South Africa is the seventh largest producer of iron ore in the world. Iron has been mined in South Africa for thousands of years. Evidence of early mining activities was found in archaeological sites dating back to the Iron Age around 770 AD.
.
Iron is extracted from ore using a blast furnace. Iron ore, a type of coal called coke (which contains [latex]\scriptsize \displaystyle 85\%[/latex] carbon) and lime are added to the top of the blast furnace. Hot air provides the oxygen for the reaction. The temperature of a blast furnace can be up to [latex]\scriptsize \displaystyle 1\text{ }200\text{ }{}^\circ \text{C}[/latex]. The reaction takes place inside the furnace and molten iron is removed from the bottom. Lime (calcium carbonate) is added to react with the unwanted materials, such as sand (silicon dioxide). This produces a waste product called slag. The slag is removed from the bottom and used for building roads. Iron is used to make steel. In 2020, South Africa’s production of iron ore amounted to an estimated [latex]\scriptsize \displaystyle 71[/latex] million metric tons. South Africa is one of the world’s largest producers of iron ore.Figure 7: A blast furnace - Gold: One of the largest gold companies in the world, AngloGold Ashanti, headquartered in Johannesburg, was founded in 2004. AngloGold Ashanti generated revenues of [latex]\scriptsize \displaystyle 4.43[/latex] billion in 2020. It produced over three million ounces of gold in 2020, with over half of it being produced in Africa. Two of the deepest gold mines worldwide are situated in South Africa. These are the AngloGold Ashanti’s Mponeng gold mine that is [latex]\scriptsize \displaystyle 4[/latex] kilometres deep as well as TauTona, which is also part of the AngloGold Ashanti mines. It extends beyond [latex]\scriptsize \displaystyle 3.9[/latex] kilometres.
- Platinum: Total worldwide reserves of platinum metals are estimated to be some [latex]\scriptsize \displaystyle 69\text{ }000[/latex] metric tons. [latex]\scriptsize \displaystyle 95\%[/latex] is in the Earth’s crust in South Africa. Platinum in most cases is a by-product of copper and nickel mines and refineries. The largest pure platinum mines are in South Africa, which is also the world’s leading producer of the element. Around [latex]\scriptsize \displaystyle 120[/latex] metric tons were produced there in 2020.
Bathopele mine is one of the largest platinum mines with reserves of up to [latex]\scriptsize \displaystyle 5.3[/latex] million ounces (oz) and a production of [latex]\scriptsize \displaystyle 120\text{ }000[/latex]oz of platinum yearly. It is situated in Rustenburg.
The largest platinum mining company worldwide is South Africa’s Anglo American Platinum Ltd., headquartered in Johannesburg. Other leading platinum companies are Impala Platinum (South Africa), Sibanye Gold Ltd. (South Africa), and Lonmin (United Kingdom).
Platinum is used for vehicle emission control devices and jewellery but is also in high demand for laboratory devices and as an investment. - Diamonds: Diamond is probably one of the most valuable minerals in South Africa, being a valuable and majorly sought-after precious stone. South Africa’s diamond production amounted to [latex]\scriptsize \displaystyle 7.2[/latex] million carats, positioning it as the world’s sixth-largest diamond producer.
- Coal: South Africa is one of the top five coal exporting countries worldwide. Almost one quarter of the coal mined in the country gets exported making it the third largest foreign income earner for the state. The coal mine companies include South32’s South Africa Energy Coal, Sasol Mining, Anglo American PLC, Exxaro and Glencore Xstrata.
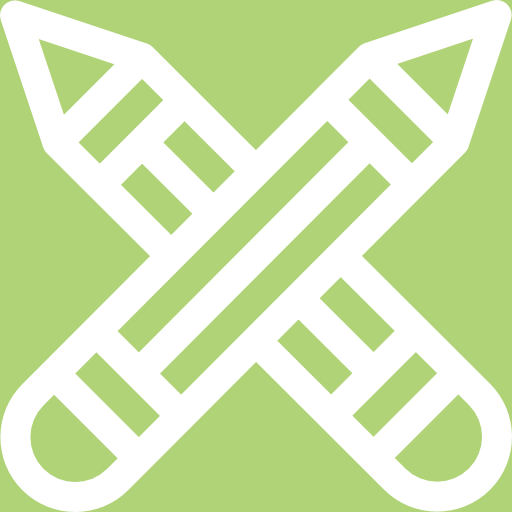
Exercise 1.2
- List two uses of the metal iron.
- Name three minerals mined in South Africa which are used to make jewellery.
- Suggest a reason why gold mining is declining in South Africa.
The full solutions are at the end of the unit
Cement
PPC and Lafarge are the two largest cement manufacturers in South Africa. PPC has 11 cement factories in Southern Africa. PPC’s capacity is around 11.5 million tonnes of cement products each year and it has 26 batching plants across South Africa. PPC also produces aggregates with its Mooiplaas aggregates quarry in Gauteng having the largest aggregate production capacity in South Africa. Lafarge has 19 aggregate quarries in South Africa and manufactures cement in several locations.
Cement is a binder and is used for construction as it sets, hardens, and adheres to other materials to bind them together. Cement is seldom used on its own, but to bind sand and gravel (aggregate) together. Cement mixed with fine aggregate produces mortar for masonry, or with sand and gravel, produces concrete. Concrete is the most widely used material in existence and is behind only water as the planet’s most-consumed resource.
Cements used in construction are usually inorganic, often lime or calcium silicate based, which can be characterised as non-hydraulic or hydraulic respectively, depending on the ability of the cement to set in the presence of water.
Non-hydraulic cement does not set in wet conditions or under water. Rather, it sets as it dries and reacts with carbon dioxide in the air. It is resistant to attack by chemicals after setting.
Hydraulic cements (e.g. Portland cement) set and become adhesive due to a chemical reaction between the dry ingredients and water. The chemical reaction results in mineral hydrates that are not very water-soluble and so are quite durable in water and safe from chemical attack. This allows setting in wet conditions or under water and further protects the hardened material from chemical attack.
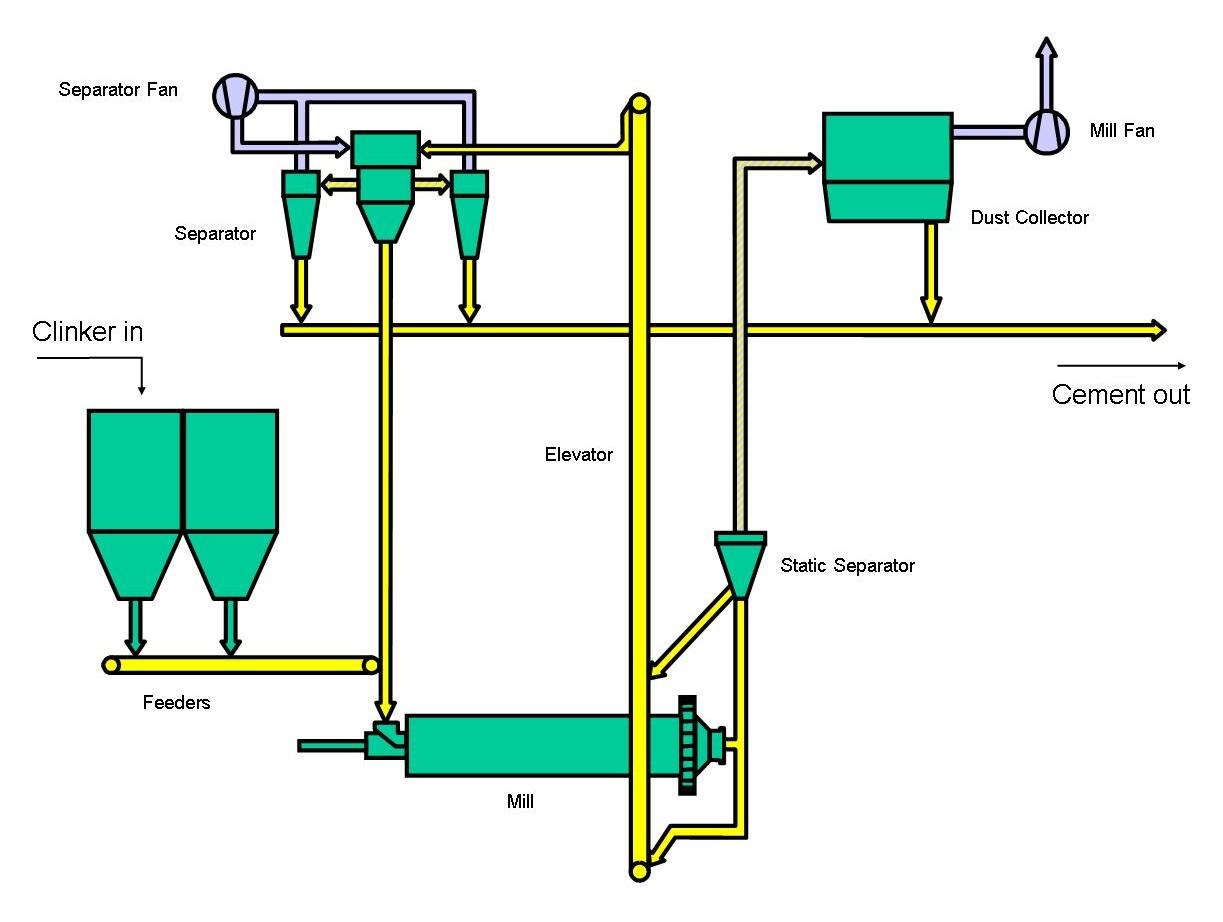
Cement is manufactured through a controlled chemical combination of calcium, silicon, aluminium, iron, and other ingredients. Common materials used to manufacture cement include limestone, shells, and chalk or marl combined with shale, clay, slate, blast furnace slag, silica sand, and iron ore. These ingredients, when heated at high temperatures form a rock-like substance that is ground into the fine powder that we commonly think of as cement. Concrete is formed when Portland cement creates a paste with water that binds with sand and rock to harden.
Note
To understand how cement is made you can visit the site www.howcementismade.com and interact with a 3-D cement plant.
Explosives
Explosives are also manufactured in South Africa. Explosives are used in underground mines and quarries to break coal and other rocks. An explosive is a solid or a liquid substance or mixture of substances which change themselves instantaneously into a large volume of gases at high temperature and pressure when a flame, heat, or sudden shock (detonation) is applied to it. Detonation is a process of giving a sufficiently violent shock to the explosive to bring about an almost instantaneous rearrangement of atoms.
The chemical energy in an explosive is released and converted suddenly into heat and mechanical energy when heat, flame or detonation is applied, and this conversion is due to a chemical reaction which is essentially a process of oxidation. An explosive contains enough oxygen necessary for complete oxidation.
Explosives are grouped in two types depending upon the speed with which the explosive effect is produced: low explosives and high explosives.
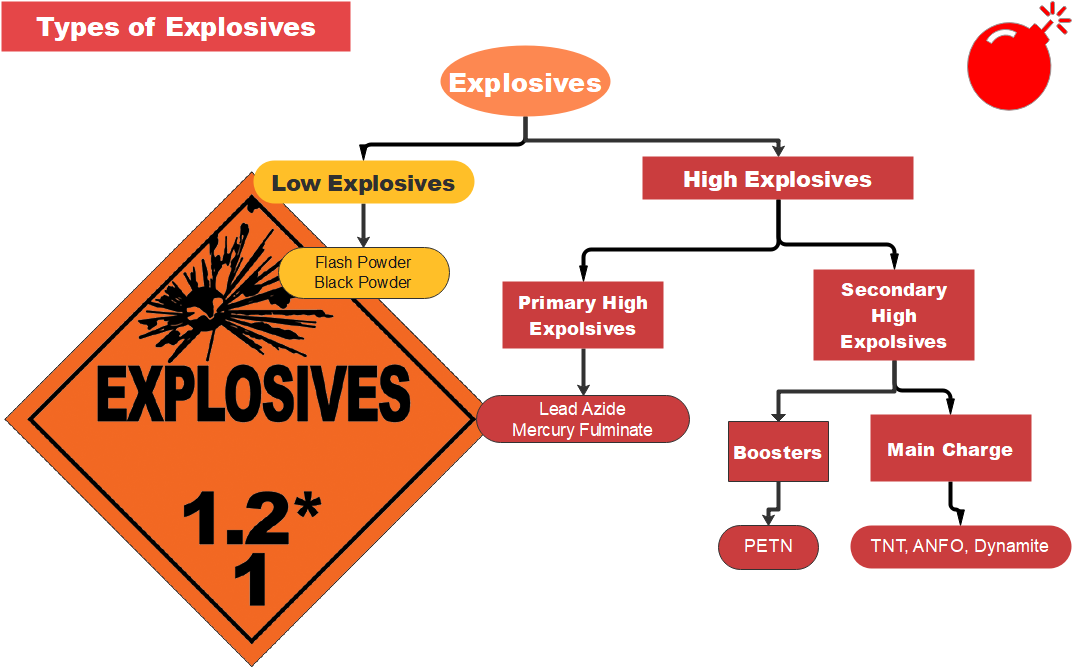
When a low explosive is blasted, it is spread by rapid combustion and the effect of explosion is low. A low explosive is fired by ignition or a flame. High explosives always contain an ingredient which is explosive in itself, at least when sensitised by proper means. A high explosive explodes when a violent shock is applied to it with the help of a detonator; the explosion is instantaneous and reacts with high velocity. High explosives therefore produce a shattering effect.
Ammonium nitrate consumption for explosives has grown because of its safety advantage over other products such as dynamite. Ammonium nitrate can be shipped and stored and mixed with fuel oil when needed. Ammonium nitrate fuel oil (ANFO) is made of about [latex]\scriptsize 94\%[/latex] ammonium nitrate and [latex]\scriptsize 6\%[/latex] fuel oil. ANFO is widely used as an explosive in mining, quarrying, and tunnelling construction or wherever dry conditions exist.
AECI has been manufacturing explosives for mining in Modderfontein, Gauteng since 1895. AECI make blasting caps and detonation fuse wires specifically for the mining industry.
Fertiliser
Plants are only able to absorb nutrients from the soil when they are dissolved in water so that their root systems can absorb the nutrients. Nitrogen gas ([latex]\scriptsize \displaystyle {{\text{N}}_{\text{2}}}[/latex]) for example, cannot be absorbed in the gas form, and needs to be changed into an ion that is soluble in water, for example the nitrate ion ([latex]\scriptsize \displaystyle \text{NO}_{3}^{-}[/latex]). In the same way phosphorus is absorbed as phosphate ions ([latex]\scriptsize \displaystyle \text{PO}_{\text{4}}^{{\text{3-}}}[/latex]).
Fertilisers usually provide the three major plant nutrients (nitrogen, phosphorus, and potassium). Fertilisers are in general applied to the soil so that the nutrients are absorbed by plants through their roots. Often, cultivation practices do not give the soil enough time to recover and to replace the nutrients that have been lost naturally. Today, fertilisers play an important role in restoring soil nutrients so that crop yields can stay high. Some of these fertilisers are organic (e.g. compost, manure, and fishmeal). Industrial fertilisers are inorganic (for example ammonium nitrate ([latex]\scriptsize \displaystyle \text{N}{{\text{H}}_{\text{4}}}\text{N}{{\text{O}}_{\text{3}}}[/latex]) or super phosphates ([latex]\scriptsize \displaystyle \text{Ca}{{\left( {{{\text{H}}_{\text{2}}}\text{P}{{\text{O}}_{\text{4}}}} \right)}_{\text{2}}}[/latex]) and have the advantage of being in a soluble form that can be absorbed by a plant immediately.
Fertiliser packaging contains a set of numbers, for example [latex]\scriptsize \displaystyle 6:1:5[/latex]. These numbers are called the NPK ratio, and they give the mass ratio of nitrogen, phosphorus, and potassium in the fertiliser. The NPK ratio expresses the content of each nutrient as a percentage of N, P and K in this order. A number in brackets after this ratio indicates the percentage by mass of N, P and K that is present in the fertiliser (what percentage of the total fertiliser is N, P and K). For example, in:
[latex]\scriptsize \begin{align*}&\text{N P K}\\&\text{3 1 5 (38)}\end{align*}[/latex]
[latex]\scriptsize \displaystyle 38\%[/latex] of the total fertiliser is nitrogen, phosphorus, or potassium
% N: [latex]\scriptsize \displaystyle 3[/latex] in every [latex]\scriptsize \displaystyle ~9[/latex] parts of the [latex]\scriptsize 38\%[/latex] contains nitrogen (N)
% P: [latex]\scriptsize \displaystyle 1[/latex] in every [latex]\scriptsize \displaystyle 9[/latex] parts of the [latex]\scriptsize 38\%[/latex] contains phosphorus (P)
% K: [latex]\scriptsize \displaystyle 5[/latex] in every [latex]\scriptsize \displaystyle 9[/latex] parts of the [latex]\scriptsize 38\%[/latex] contains potassium (K)
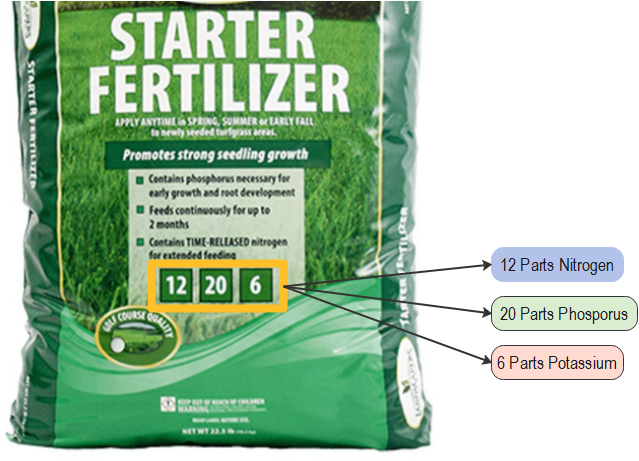
Depending on the types of plants you are growing, and the growth stage they are in, you may need to use a fertiliser with a slightly different ratio. For example, if you want to encourage root growth in your plant you might choose a fertiliser with a greater ratio of phosphorus in it. The main functions are summarised in the table below.
Nutrient | Promotes | When to use |
Nitrogen (N) | leafy plant growth, faster plant growth | on lawns and other plants with lots of green leaves |
Phosphorus (P) | strong roots, healthy fruit, blooming | on flowers and flower beds |
Potassium (K) | disease resistance, growth of fruit | on fruit bearing plants |
Some countries express the phosphorus content as [latex]\scriptsize \displaystyle ~{{\text{P}}_{\text{2}}}{{\text{O}}_{\text{5}}}[/latex] and potassium content as [latex]\scriptsize \displaystyle {{\text{K}}_{\text{2}}}\text{O}[/latex]. South Africa expresses the NPK ratio in terms of the elements present as explained above. The rest of the fertiliser ([latex]\scriptsize \displaystyle 62\%[/latex]) is made up of fillers, such as gypsum, lime, and sand. Other micronutrients, such as calcium (Ca), sulfur (S) and magnesium (Mg), are often added to the mixture.
The manufacture of fertilisers
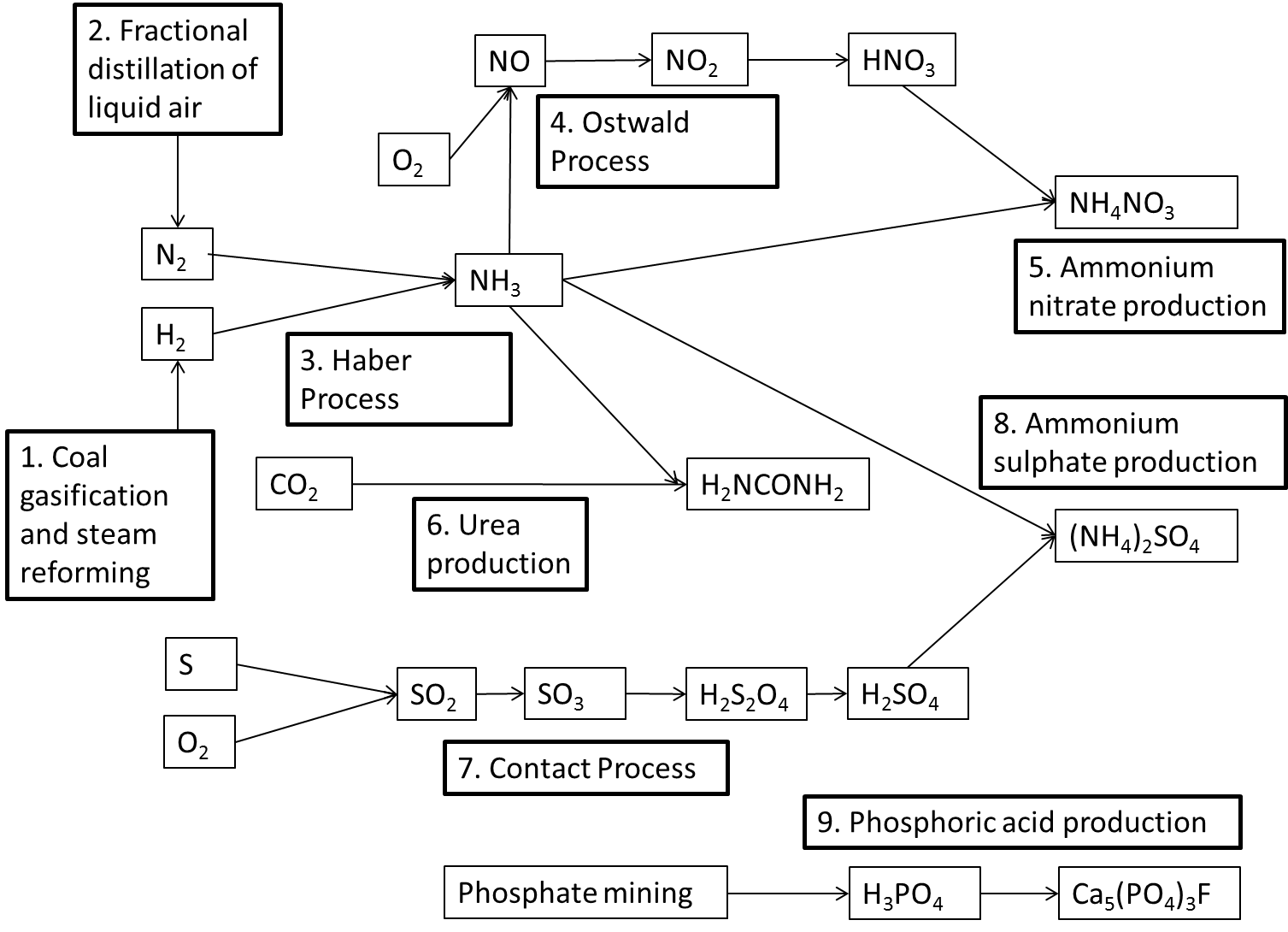
Various chemicals are needed to make fertilisers, namely hydrogen, nitrogen and ammonia.
- Obtaining hydrogen: Fossil fuels are the main source of industrial hydrogen. Hydrogen can be generated from natural gas or coal. These processes are used by Sasol at their Gas-to-Liquid (GTL) and Coal-to-Liquid (CTL) facilities. Hydrogen is usually produced by the steam reforming of methane gas (natural gas). At high temperatures ([latex]\scriptsize 700\text{ }\!\!{}^\circ\!\!\text{ C} - 1~100\text{ }\!\!{}^\circ\!\!\text{ C}[/latex]), steam ([latex]\scriptsize \displaystyle {{\text{H}}_{\text{2}}}\text{O}[/latex]) reacts with methane ([latex]\scriptsize \displaystyle \text{C}{{\text{H}}_{\text{4}}}[/latex]) in an endothermic reaction to yield syngas, a mixture of carbon monoxide (CO) and hydrogen ([latex]\scriptsize \displaystyle {{\text{H}}_{\text{2}}}[/latex]).
.
[latex]\scriptsize \displaystyle \text{C}{{\text{H}}_{{\text{4}\left( \text{g} \right)}}}\text{+}{{\text{H}}_{\text{2}}}{{\text{O}}_{{\left( \text{g} \right)}}}\to \text{C}{{\text{O}}_{{\left( \text{g} \right)}}}\text{+3}{{\text{H}}_{{\text{2}\left( \text{g} \right)}}}[/latex]
.
During a second stage, which takes place at a lower temperature of about [latex]\scriptsize \displaystyle 130\text{ }\!\!{}^\circ\!\!\text{ C}[/latex], the exothermic reaction generates additional hydrogen. This is called a water gas shift reaction. Essentially, the oxygen (O) atom is stripped from the additional water (steam) to oxidise CO to [latex]\scriptsize \displaystyle \text{C}{{\text{O}}_{\text{2}}}[/latex]. This oxidation also provides energy to maintain the reaction. - Obtaining nitrogen: Fractional distillation is a separation method. It uses the difference in boiling temperatures of the components of a mixture to separate those components. A mixture is heated to convert the components into the vapour (gas) phase. The vapour mixture is then pumped into a tall separation column (called a fractional distillation column), usually at the bottom of the column. As the vapour mixture moves up the column and cools, the different components (called fractions) condense as the temperature drops below the various boiling point temperatures.
.
Air is a mixture of gases, mainly nitrogen and oxygen. Liquefied air (compressed and cooled to [latex]\scriptsize \displaystyle \text{-200 }\!\!{}^\circ\!\!\text{ C}[/latex]) is pumped into the fractional distillation column. Nitrogen gas has the lowest boiling point temperature and is collected at the top of the column. - Producing ammonia and nitric acid: Ammonia ([latex]\scriptsize \displaystyle \text{N}{{\text{H}}_{\text{3}}}[/latex]) plays an important role in the manufacturing process of fertilisers. The industrial process used to produce ammonia is called the Haber process. In this reaction nitrogen gas and hydrogen gas react to produce ammonia gas. The equation for the Haber process is:
.
[latex]\scriptsize \displaystyle {{\text{N}}_{{\text{2}\left( \text{g} \right)}}}\text{+3}{{\text{H}}_{{\text{2}\left( \text{g} \right)}}}\rightleftharpoons \text{2N}{{\text{H}}_{{\text{3}\left( \text{g} \right)}}}[/latex]
.
This reaction takes place in the presence of an iron catalyst under high pressure ([latex]\scriptsize \displaystyle 200[/latex] atmospheres (atm)) and temperature ([latex]\scriptsize 450\text{ }\!\!{}^\circ\!\!\text{ C} - 500\text{ }\!\!{}^\circ\!\!\text{ C}[/latex]) conditions.
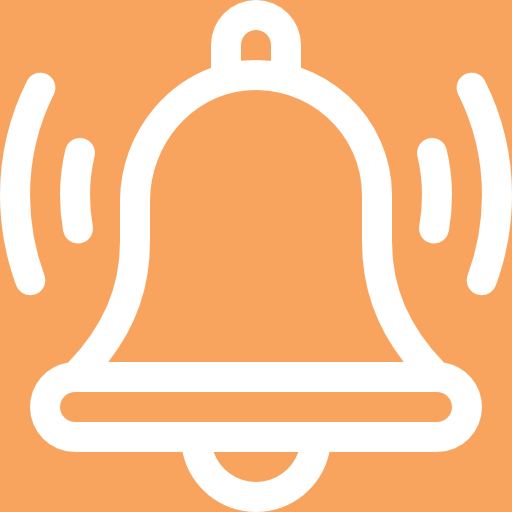
Take note!
The forward reaction of the Haber process is exothermic, so the forward reaction is favoured by low temperatures. However, low temperatures slow all chemical reactions. So as the Haber process requires high temperatures, the ammonia is removed as soon as it is formed to prevent it being used in the reverse reaction.
The Ostwald process is used to produce nitric acid from ammonia. Nitric acid can then be used in reactions that produce fertilisers. Ammonia is converted to nitric acid in a three-step process.
Firstly ammonia is oxidised by heating it with oxygen, in the presence of a platinum (Pt) catalyst, to form nitrogen monoxide (NO) and water. This step is strongly exothermic, which makes it a useful heat source. The reaction that takes place is:
[latex]\scriptsize \displaystyle \text{4N}{{\text{H}}_{{\text{3}\left( \text{g} \right)}}}\text{+5}{{\text{O}}_{{\text{2}\left( \text{g} \right)}}}\to \text{4N}{{\text{O}}_{{\left( \text{g} \right)}}}\text{+6}{{\text{H}}_{\text{2}}}{{\text{O}}_{{\left( \text{g} \right)}}}[/latex]
Secondly, nitrogen monoxide is oxidised again to yield nitrogen dioxide ([latex]\scriptsize \displaystyle \text{N}{{\text{O}}_{\text{2}}}[/latex]) according to the following reaction:
[latex]\scriptsize \displaystyle \text{2N}{{\text{O}}_{{\left( \text{g} \right)}}}\text{+}{{\text{O}}_{{\text{2}\left( \text{g} \right)}}}\to \text{2N}{{\text{O}}_{{\text{2}\left( \text{g} \right)}}}[/latex]
Thirdly, nitrogen dioxide is absorbed by water to produce nitric acid ([latex]\scriptsize \displaystyle \text{HN}{{\text{O}}_{\text{3}}}[/latex]) as follows:
[latex]\scriptsize \displaystyle \text{3N}{{\text{O}}_{{\text{2}\left( \text{g} \right)}}}\text{+}{{\text{H}}_{\text{2}}}{{\text{O}}_{{\left( \text{l} \right)}}}\to \text{2HN}{{\text{O}}_{{\text{3}\left( {\text{aq}} \right)}}}\text{+N}{{\text{O}}_{{\left( \text{g} \right)}}}[/latex]
Nitrogen monoxide is a by-product of this reaction and is recycled, and the acid is concentrated to the required strength.
Nitric acid and ammonia can react together in an acid-base process to form the salt, ammonium nitrate [latex]\scriptsize \displaystyle \left( {\text{N}{{\text{H}}_{\text{4}}}\text{N}{{\text{O}}_{\text{3}}}} \right)[/latex]. Ammonium nitrate is soluble in water and is often used in fertilisers. The reaction is as follows: [latex]\scriptsize \displaystyle \text{N}{{\text{H}}_{{\text{3}\left( \text{l} \right)}}}\text{+HN}{{\text{O}}_{{\text{3}\left( \text{l} \right)}}}\to \text{N}{{\text{H}}_{\text{4}}}\text{N}{{\text{O}}_{{\text{3}\left( \text{s} \right)}}}[/latex].
Ammonium nitrate is used to make fertilisers and explosives.
Note
To consolidate your understanding of how fertilisers work, watch this video by the agriculture academy called How fertilisers work.
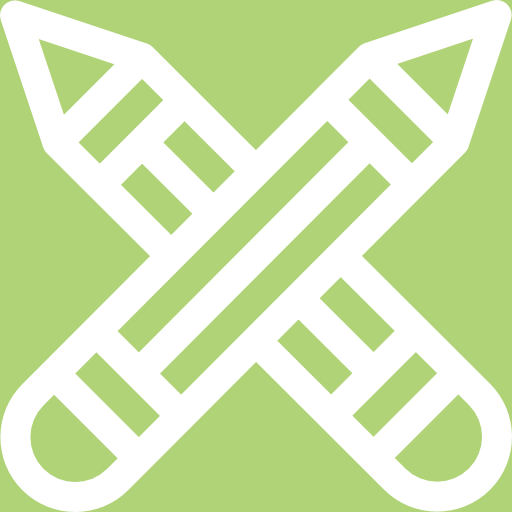
Exercise 1.3
- A bag of fertiliser has the following information on it: [latex]\scriptsize \displaystyle 3-1-6\text{ }\left( {35} \right)[/latex].What percentage of the fertiliser is composed of nitrogen, phosphorus, and potassium?
- Consider only the percentage of the fertiliser that is composed of nitrogen, phosphorus, and potassium. In a sample of [latex]\scriptsize \displaystyle 10[/latex] units, how many units are nitrogen, how many units are phosphorus and how many units are potassium?
- Why does a plant need:
- nitrogen
- phosphorus
- potassium
- Which one of the following pairs of reactants is used in a reaction during the Haber process?
- [latex]\scriptsize \displaystyle {{\text{H}}_{{\text{2}\left( \text{g} \right)}}}[/latex]and [latex]\scriptsize \displaystyle {{\text{N}}_{{\text{2}\left( \text{g} \right)}}}[/latex]
- [latex]\scriptsize \displaystyle \text{S}{{\text{O}}_{{\text{3}\left( \text{g} \right)}}}[/latex]and [latex]\scriptsize \displaystyle {{\text{O}}_{{\text{2}\left( \text{g} \right)}}}[/latex]
- [latex]\scriptsize \displaystyle \text{N}{{\text{O}}_{{\left( \text{g} \right)}}}[/latex]and [latex]\scriptsize \displaystyle {{\text{O}}_{{\text{2}\left( \text{g} \right)}}}[/latex]
- [latex]\scriptsize \displaystyle {{\text{H}}_{\text{2}}}{{\text{O}}_{{\left( \text{l} \right)}}}[/latex]and [latex]\scriptsize \displaystyle {{\text{H}}_{\text{2}}}{{\text{S}}_{\text{2}}}{{\text{O}}_{{\text{7}\left( \text{l} \right)}}}[/latex]
The full solutions are at the end of the unit.
The chloralkali Industry
The chlorine-alkali (chloralkali) industry is an important part of the chemical industry, which produces chlorine and sodium hydroxide through the electrolysis of the raw material brine. Brine is a saturated solution of sodium chloride (NaCl) that is obtained from natural salt deposits.
Remember that electrolytic cells are used to transform reactants into products by turning electric current into chemical potential energy.
The products of the chloralkali industry have a number of important uses.
Chlorine is used:
- to purify water
- as a disinfectant.
Chlorine is used in the production of:
- hypochlorous acid (used to kill bacteria in drinking water)
- paper
- food
- antiseptics, insecticides, medicines, textiles, laboratory chemicals
- paints, petroleum products, solvents, plastics (such as polyvinyl chloride).
Chlorine is the chemical most often used to keep swimming pools and jacuzzis free of bacteria that can be hazardous to humans. The chlorine breaks down into many different chemicals, including hypochlorous acid [latex]\scriptsize \displaystyle \left( {\text{HOCl}} \right)[/latex] and hypochlorite ions [latex]\scriptsize \displaystyle \left( {\text{OC}{{\text{l}}^{\text{-}}}} \right)[/latex]. Both kill microorganisms and bacteria by attacking the cell walls and destroying the enzymes and structures inside the cell, making them harmless.
Sodium hydroxide (also known as ‘caustic soda’) is used to:
- make soap and other cleaning agents
- purify bauxite (the ore of aluminium)
- make paper
- make rayon (artificial silk).
One of the problems of producing chlorine and sodium hydroxide is that when they are produced together the chlorine combines with the sodium hydroxide to form chlorate ([latex]\scriptsize \displaystyle \text{Cl}{{\text{O}}^{\text{-}}}[/latex]) and chloride ([latex]\scriptsize \displaystyle \text{C}{{\text{l}}^{\text{-}}}[/latex]) ions. This leads to the production of sodium chlorate, [latex]\scriptsize \displaystyle \text{NaClO}[/latex], a component of household bleach.
To overcome this problem the chlorine and sodium hydroxide must be separated from each other so that they do not react. There are three industrial processes that have been designed to overcome this problem. All three methods involve electrolytic cells.
The mercury cell method
A mercury cell is an electrolytic cell.
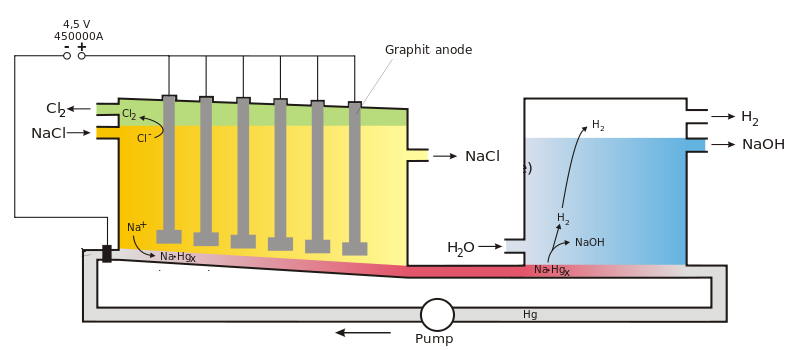
At the anode side, the anodes are placed in the aqueous [latex]\scriptsize \displaystyle \text{NaCl}[/latex] solution, above the liquid mercury. The reduction of [latex]\scriptsize \displaystyle \text{C}{{\text{l}}^{\text{-}}}[/latex] occurs to produce chlorine gas, [latex]\scriptsize \displaystyle \text{C}{{\text{l}}_{{\text{2}\left( \text{g} \right)}}}[/latex].
At the cathode side, a layer of [latex]\scriptsize \displaystyle \text{H}{{\text{g}}_{{\left( \text{l} \right)}}}[/latex] at the bottom of the tank serves as the cathode. With a mercury cathode, the reaction of [latex]\scriptsize \displaystyle {{\text{H}}_{\text{2}}}{{\text{O}}_{{\left( \text{l} \right)}}}[/latex] to [latex]\scriptsize \displaystyle {{\text{H}}_{\text{2}}}[/latex] has a fairly high over potential, so the reduction of [latex]\scriptsize \displaystyle \text{N}{{\text{a}}^{\text{+}}}[/latex] to [latex]\scriptsize \displaystyle \text{Na}[/latex] occurs instead. The [latex]\scriptsize \displaystyle \text{Na}[/latex] is soluble in [latex]\scriptsize \displaystyle \text{H}{{\text{g}}_{{\left( \text{l} \right)}}}[/latex] and the two combine to form the [latex]\scriptsize \displaystyle \text{Na-Hg}[/latex] alloy amalgam. This amalgam can be removed and then mixed with water to cause the following reaction:
[latex]\scriptsize \displaystyle \text{2Na}\left( {\text{in Hg}} \right)\text{+2}{{\text{H}}_{\text{2}}}\text{O}\to \text{2N}{{\text{a}}^{\text{+}}}\text{+2O}{{\text{H}}^{\text{-}}}\text{+}{{\text{H}}_{{\text{2}\left( \text{g} \right)}}}\text{+H}{{\text{g}}_{{\left( \text{l} \right)}}}[/latex]
The [latex]\scriptsize \displaystyle \text{H}{{\text{g}}_{{\left( \text{l} \right)}}}[/latex] that forms, is recycled back into the liquid at the bottom of the tank that acts as a cathode.
[latex]\scriptsize \displaystyle {{\text{H}}_{\text{2}}}[/latex] gas is released. [latex]\scriptsize \displaystyle \text{NaOH}[/latex] is left in a very pure, aqueous form.
This method only produces a fraction of the chlorine and sodium hydroxide that is used by industry as it has certain disadvantages:
- mercury is expensive and toxic
- some mercury always escapes with the brine that has been used
- mercury reacts with the brine to form mercury(II) chloride
- the mercury cell requires a lot of electricity
- although the chlorine gas produced is very pure, mercury must be removed from the sodium hydroxide and hydrogen gas mixture. In the past the effluent was released into lakes and rivers, causing mercury to accumulate in fish and other animals feeding on the fish. Today, the brine is treated before it is discharged so that the environmental impact is lower.
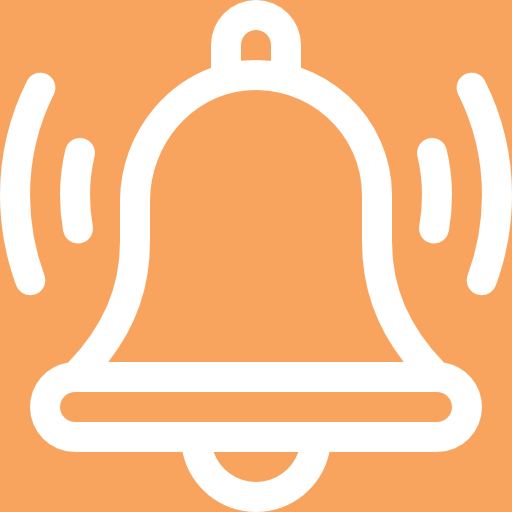
Take note!
If chlorine comes into contact with hydrogen, it produces a mixture which will explode violently on exposure to sunlight or heat. Hydrogen chloride gas would be produced. Obviously, the two gases need to be kept apart.
The diaphragm cell method
The diaphragm cell is another electrolytic cell.
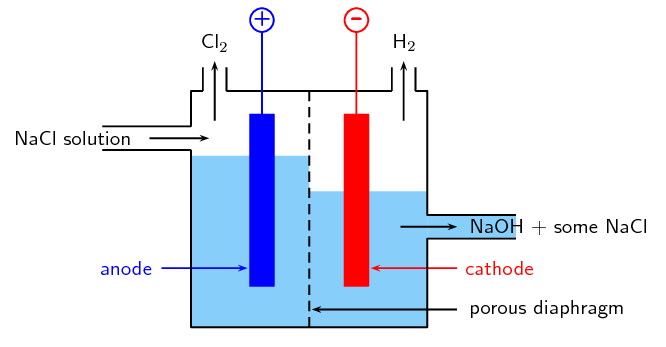
In a diaphragm cell:
- a porous diaphragm made of asbestos divides the electrolytic cell into an anode compartment and a cathode compartment
- brine is introduced into the anode compartment and flows through the diaphragm into the cathode compartment
- an electric current is passed through the brine causing the salt’s chlorine ions and sodium ions to move to the electrodes
- Chlorine gas is produced at the anode: [latex]\scriptsize \displaystyle \text{2C}{{\text{l}}^{\text{-}}}_{{\left( {\text{aq}} \right)}}\text{+ 2}{{\text{e}}^{\text{-}}}\to \text{C}{{\text{l}}_{{\text{2}\left( \text{g} \right)}}}[/latex]
- At the cathode, sodium ions react with water forming caustic soda (NaOH) and hydrogen gas: [latex]\scriptsize \displaystyle \text{2N}{{\text{a}}^{\text{+}}}_{{\left( {\text{aq}} \right)}}\text{+ 2}{{\text{H}}_{\text{2}}}{{\text{O}}_{{\left( \text{l} \right)}}}\text{+}{{\text{e}}^{\text{-}}}\to \text{2NaO}{{\text{H}}_{{\left( {\text{aq}} \right)}}}\text{+}{{\text{H}}_{{\text{2}\left( \text{g} \right)}}}[/latex]
- Some NaCl salt remains in the solution with the caustic soda and can be removed at a later stage.
The advantages of the diaphragm cell are:
- it uses less energy than a mercury cell
- it does not contain toxic mercury.
It also has disadvantages however:
- the sodium hydroxide is much less concentrated and not as pure
- the chlorine gas often contains oxygen gas as well
- the process is less cost-effective as the sodium hydroxide solution needs to be concentrated and purified before it can be used
- asbestos poses health risks to workers.
The membrane cell method
A third way to make even more pure [latex]\scriptsize \displaystyle \text{NaOH}[/latex] is to use a membrane cell. It is preferred over the diaphragm cell or mercury cell methods because it uses the least amount of electric energy and produces the highest quality [latex]\scriptsize \displaystyle \text{NaOH}[/latex]. An ion-permeable membrane is used to separate the anode and cathode.
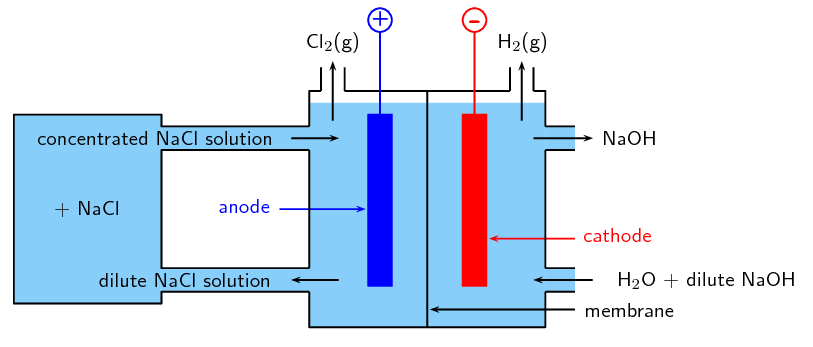
At the anode, saturated brine is fed to the compartment containing [latex]\scriptsize \displaystyle \text{N}{{\text{a}}^{\text{+}}}[/latex] and [latex]\scriptsize \displaystyle \text{C}{{\text{l}}^{\text{-}}}[/latex]. Chloride ions are oxidised to chlorine gas at the anode.
[latex]\scriptsize \displaystyle \text{2C}{{\text{l}}^{\text{-}}}_{{\left( {\text{aq}} \right)}}\text{+ 2}{{\text{e}}^{\text{-}}}\to \text{C}{{\text{l}}_{{\text{2}\left( \text{g} \right)}}}[/latex]
The chlorine is purified by liquifying it under pressure. The oxygen stays as a gas when it is compressed at ordinary temperatures. The membrane allows [latex]\scriptsize \displaystyle \text{N}{{\text{a}}^{\text{+}}}[/latex] ions to pass into the cathode compartment.
At the cathode, [latex]\scriptsize \displaystyle {{\text{H}}_{\text{2}}}\text{O}[/latex] is reduced to form [latex]\scriptsize \displaystyle \text{O}{{\text{H}}^{\text{-}}}[/latex] and [latex]\scriptsize \displaystyle {{\text{H}}_{\text{2}}}[/latex] gas: [latex]\scriptsize \displaystyle \text{2}{{\text{H}}_{\text{2}}}\text{O}\to {{\text{H}}_{\text{2}}}\text{+2O}{{\text{H}}^{\text{-}}}[/latex].
[latex]\scriptsize \displaystyle \text{N}{{\text{a}}^{\text{+}}}[/latex] ions that had flowed through the membrane and [latex]\scriptsize \displaystyle \text{O}{{\text{H}}^{\text{-}}}[/latex] produced through the reduction of water react to form aqueous [latex]\scriptsize \displaystyle \text{NaOH}[/latex]. [latex]\scriptsize \displaystyle {{\text{H}}_{\text{2}}}[/latex] gas also is produced as a by-product.
The membrane is made from a polymer which only allows positive ions to pass through it. That means that the only the sodium ions from the sodium chloride solution can pass through the membrane, and not the chloride ions. The advantage of this is that the sodium hydroxide solution being formed in the right-hand compartment never gets contaminated with any sodium chloride solution. The sodium chloride solution being used must be pure. If it contains any other metal ions, these would also pass through the membrane and so contaminate the sodium hydroxide solution.
[latex]\scriptsize \displaystyle \text{2NaC}{{\text{l}}_{{\left( {\text{aq}} \right)}}}\text{+2}{{\text{H}}_{\text{2}}}{{\text{O}}_{{\left( \text{l} \right)}}}\text{ }\to \text{C}{{\text{l}}_{{\text{2}\left( \text{g} \right)}}}\text{+}{{\text{H}}_{{\text{2}\left( \text{g} \right)}}}\text{+2NaO}{{\text{H}}_{{\text{(g)}}}}[/latex]
The advantages of using this method are:
- the sodium hydroxide that is produced is very pure because chloride ions cannot pass through the membrane and contaminate it
- the sodium hydroxide has a relatively high concentration
- this process uses the least electricity of all three cells
- the cell is cheaper to operate than the other two cells
- the cell does not contain toxic mercury or asbestos.
Note
To further understand the chloralkali industry, watch this video by Fuse Schools, called The Brine Industry.
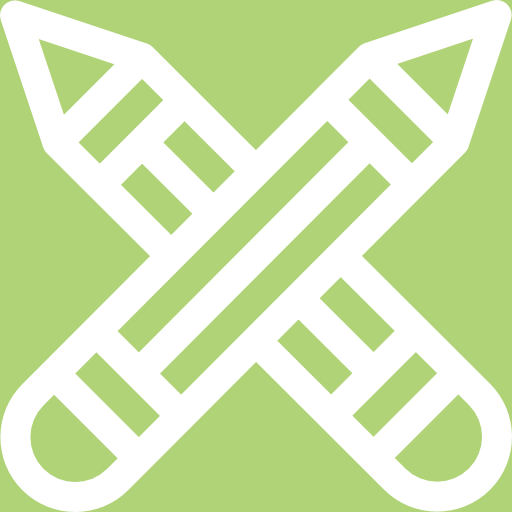
Exercise 1.4
- Summarise what you have learnt about the three types of cells in the chloralkali industry by copying and completing the table below:
Mercury cell Diaphragm cell Membrane cell Main raw material Mechanism of separating where [latex]\scriptsize \displaystyle \text{C}{{\text{l}}_{\text{2}}}[/latex] and [latex]\scriptsize \displaystyle \text{NaOH}[/latex] are produced Anode reaction Cathode reaction Purity of NaOH produced Purity of [latex]\scriptsize \displaystyle \text{C}{{\text{l}}_{\text{2}}}[/latex] produced Energy consumption Environmental impact Cost of production - The diagram below shows the sequence of steps that take place in a mercury cell.
- Name the ‘raw material’ in step 1.
- Give the chemical equation for the reaction that produces chlorine gas in step 2.
- What other product is formed in step 2.
- Name the reactants in step 4.
The full solutions are at the end of the unit.
Summary
In this unit you have learnt the following:
- The growth of South Africa’s chemical industry was largely due to the mining industry, which requires explosives for their operation. One of South Africa’s major chemical companies is Sasol. Other important examples of chemical industries in the country are the chloralkali and fertiliser industries.
- The Fisher-Tröpsch process is used by Sasol to convert coal to liquid fuels
- Other products made from this process include heavy waxes, organic liquids, and chemical feedstocks.
- South Africa has many mineral resources which are mined from the ground.
- These mined minerals include iron ore, coal, gold, platinum, and diamonds.
- Iron ore is processed in blast furnaces to produce pure iron which is used to make steel.
- South Africa has a large paint, cement, and adhesive industry.
- The fertiliser industry is very important in providing fertilisers with the correct nutrients in the correct quantities to ensure maximum growth for various plants and crops.
- Fertilisers can be produced industrially using several chemical processes: the Haber process reacts nitrogen and hydrogen to produce ammonia; the Ostwald process reacts oxygen and ammonia to produce nitric acid.
- Ammonium nitrate produced from the Ostwald process is used by companies like AECI to manufacture explosives.
- The chloralkali industry produces sodium hydroxide and chlorine.
- Chlorine is used to make paper, as a disinfectant.
- Sodium hydroxide is used to make soap and paper.
- The production of chlorine and sodium hydroxide is done in electrolytic cells: a mercury cell, a diaphragm cell, or a membrane cell.
Unit 1: Assessment
Suggested time to complete: 20 minutes
- A bag of fertiliser has the following information on it: [latex]\scriptsize \displaystyle 18-21-6\text{ }\left( {35} \right)[/latex] and has a mass of [latex]\scriptsize \displaystyle 3\text{ kg}[/latex]. Calculate the mass of nitrogen (N), phosphorus (P) and potassium (K) that is present in the bag of fertiliser.
- You have determined that your vegetable garden will need 12 g of nitrogen. The fertiliser you have has 4:2:3 (40) written on the packet. How many grams of fertiliser will you need for your garden?
- The reaction of hydrogen and nitrogen is an exothermic reversible reaction.
- Write a balanced equation for this reaction.
Use your knowledge of chemical equilibrium and explain what effect the following will have on this equilibrium reaction: - raising the temperature
- raising the pressure.
- Write a balanced equation for this reaction.
- Refer to the flow diagram, which shows the reactions that take place in a membrane cell, and then answer the questions that follow.
- What liquid is present in the cathode compartment at A?
- Identify the gas that is produced at B.
- Explain one feature of this cell that allows the [latex]\scriptsize \displaystyle \text{N}{{\text{a}}^{\text{+}}}[/latex] and [latex]\scriptsize \displaystyle \text{O}{{\text{H}}^{\text{-}}}[/latex] ions to react at C.
- Give a balanced equation for the reaction that takes place at C.
- Approximately [latex]\scriptsize \displaystyle 30[/latex] million tonnes of chlorine are used throughout the world annually. Chlorine is produced industrially by the electrolysis of brine. The diagram represents a membrane cell used in the production of [latex]\scriptsize \displaystyle \text{C}{{\text{l}}_{\text{2}}}[/latex] gas.
- What ions are present in the electrolyte in the left-hand compartment of the cell?
- Give the equation for the reaction that takes place at the anode.
- Give the equation for the reaction that takes place at the cathode and forms a gas.
- What ion passes through the membrane while these reactions are taking place?
- Chlorine is used to purify drinking water and swimming pool water. The substance responsible for this process is the weak acid, hypochlorous acid ([latex]\scriptsize \displaystyle \text{HOCl}[/latex]). One way of putting [latex]\scriptsize \displaystyle \text{HOCl}[/latex] into a pool is to bubble chlorine gas through the water. Give an equation showing how bubbling [latex]\scriptsize \displaystyle \text{C}{{\text{l}}_{{\text{2}\left( \text{g} \right)}}}[/latex] through water produces [latex]\scriptsize \displaystyle \text{HOCl}[/latex].
The full solutions are at the end of the unit.
Unit 1: Solutions
Exercise 1.1
- .
- Coal is first converted to gas and then its hydrogenation takes place.
- An iron catalyst because the coal/gas is of a low quality.
- c. The gasoline fraction produced in Fischer-Tröpsch process is collected for further processing, while the heavy oil fractions are subjected to cracking to produce more gasoline.
Exercise 1.2
- To make steel, as a catalyst in the Fischer-Tröpsch process.
- Gold, platinum, and diamonds.
- Gold reserves are running out/gold reserves are too deep to make mining them viable.
Exercise 1.3
- The number in brackets is the percentage of the fertiliser that contains nitrogen, phosphorus, and potassium:
N:P:K (percentage)
[latex]\scriptsize \displaystyle 3\text{ }-\text{ }1\text{ }-\text{ }6\text{ }\left( {35} \right)[/latex]
In this example the percentage is [latex]\scriptsize \displaystyle 35\%[/latex] - Information about nitrogen, phosphorus and potassium is given for fertilisers as:
N:P:K (percentage)
[latex]\scriptsize \displaystyle 3\text{ }-\text{ }1\text{ }-\text{ }6\text{ }\left( {35} \right)[/latex]
The ratio of N:P:K in this fertiliser is [latex]\scriptsize \displaystyle 3:1:6.[/latex]
Therefore in 10 units of the fertiliser:
[latex]\scriptsize \displaystyle 3[/latex] units of the [latex]\scriptsize 35\%[/latex] are nitrogen
[latex]\scriptsize \displaystyle 1[/latex] unit of the [latex]\scriptsize 35\%[/latex] is phosphorus
[latex]\scriptsize \displaystyle 6[/latex] units of the [latex]\scriptsize 35\%[/latex] are potassium
Notice that these three numbers add up to [latex]\scriptsize \displaystyle 10[/latex]. - .
- leafy plant growth, faster plant growth
- strong roots, healthy fruit, blooming
- disease resistance, growth of fruit
- a
Exercise 1.4
- .
Mercury cell Diaphragm cell Membrane cell Main raw material brine brine brine Mechanism of separating reduction of [latex]\scriptsize \displaystyle \text{N}{{\text{a}}^{\text{+}}}[/latex] to Na in Hg amalgam which flows to separate compartment use of a porous asbestos diaphragm use of a membrane (charge specific) Anode reaction [latex]\scriptsize \displaystyle \text{C}{{\text{l}}^{{\text{- }\!\!~\!\!\text{ }}}}\to \text{C}{{\text{l}}_{{\text{2 }\!\!~\!\!\text{ (g)}}}}[/latex]+ 2e- [latex]\scriptsize \displaystyle \text{C}{{\text{l}}^{{\text{- }\!\!~\!\!\text{ }}}}\to \text{C}{{\text{l}}_{{\text{2 }\!\!~\!\!\text{ (g)}}}}[/latex] [latex]\scriptsize \displaystyle \text{C}{{\text{l}}^{{\text{- }\!\!~\!\!\text{ }}}}\to \text{C}{{\text{l}}_{{\text{2 }\!\!~\!\!\text{ (g)}}}}[/latex] Cathode reaction [latex]\scriptsize \displaystyle \text{2}{{\text{H}}_{\text{2}}}{{\text{O}}_{{\left( \text{l} \right)}}}\text{+2}{{\text{e}}^{\text{-}}}\to {{\text{H}}_{{\text{2}\left( \text{g} \right)}}}\text{+2O}{{\text{H}}^{\text{-}}}_{{\left( {\text{aq}} \right)}}[/latex] [latex]\scriptsize \displaystyle \text{2}{{\text{H}}_{\text{2}}}{{\text{O}}_{{\left( \text{l} \right)}}}\text{+2}{{\text{e}}^{\text{-}}}\to {{\text{H}}_{{\text{2}\left( \text{g} \right)}}}\text{+2O}{{\text{H}}^{\text{-}}}_{{\left( {\text{aq}} \right)}}[/latex] [latex]\scriptsize \displaystyle \text{2}{{\text{H}}_{\text{2}}}{{\text{O}}_{{\left( \text{l} \right)}}}\text{+2}{{\text{e}}^{\text{-}}}\to {{\text{H}}_{{\text{2}\left( \text{g} \right)}}}\text{+2O}{{\text{H}}^{\text{-}}}_{{\left( {\text{aq}} \right)}}[/latex] Purity of NaOH produced low purity medium purity, low concentration high purity Purity of [latex]\scriptsize \displaystyle \text{C}{{\text{l}}_{\text{2}}}[/latex] high purity mixed with [latex]\scriptsize \displaystyle {{\text{O}}_{\text{2}}}[/latex] mixed with [latex]\scriptsize \displaystyle {{\text{O}}_{\text{2}}}[/latex] Energy consumption high less than the mercury cell low energy Environmental impact high lower than the mercury cell, asbestos is a health hazard ower than the diaphragm and mercury cell, mercury is toxic Cost of production expensive expensive, as product must be purified low production cost - .
- aqueous sodium chloride
- [latex]\scriptsize \displaystyle \text{2C}{{\text{l}}^{\text{-}}}_{{\left( {\text{aq}} \right)}}\text{+ 2}{{\text{e}}^{\text{-}}}\to \text{C}{{\text{l}}_{{\text{2}\left( \text{g} \right)}}}[/latex]
- sodium mercury amalgam
- sodium mercury amalgam and water
Unit 1: Assessment
- T[latex]\scriptsize \displaystyle \displaystyle \frac{{\text{27}}}{{\text{0}\text{.40}}}\text{= 67}\text{.5 g}\text{.}[/latex]The ratio of N:P:K in this fertiliser is [latex]\scriptsize \displaystyle 18:21:6[/latex].
[latex]\scriptsize \displaystyle 35\%[/latex] of the sample contains nutrients. We need to convert this percent to mass as follows:
[latex]\scriptsize \displaystyle 35\%\text{ of }3\text{ kg}=\left( {0.35} \right)\left( 3 \right)=1.05\text{ kg}[/latex]. Therefore [latex]\scriptsize \displaystyle 1.05[/latex]kg of the fertiliser contains nutrients.
For every [latex]\scriptsize \displaystyle 18[/latex] units of nitrogen there are [latex]\scriptsize \displaystyle 21[/latex] units of phosphorus and [latex]\scriptsize \displaystyle 6[/latex] units of potassium so the total number of units is [latex]\scriptsize \displaystyle 45[/latex].
[latex]\scriptsize \displaystyle 18[/latex] of the [latex]\scriptsize \displaystyle 45[/latex] units are nitrogen, therefore: [latex]\scriptsize \displaystyle \displaystyle \frac{{18}}{{45}}\times 1.05=0.42\text{ kg}[/latex] will be nitrogen.
[latex]\scriptsize \displaystyle 21[/latex] of the [latex]\scriptsize \displaystyle 45[/latex] units are phosphorus, therefore: [latex]\scriptsize \displaystyle \displaystyle \frac{{21}}{{45}}\times 1.05=0.49\text{ kg}[/latex] will be phosphorus.
[latex]\scriptsize \displaystyle 6[/latex] of the [latex]\scriptsize \displaystyle 45[/latex]units are potassium, therefore: [latex]\scriptsize \displaystyle \displaystyle \frac{6}{{45}}\text{ }\!\!\times\!\!\text{ 1}\text{.05=0}\text{.14 kg}[/latex] will be potassium. - The NPK mass ratio is [latex]\scriptsize \displaystyle 4\text{ }:\text{ }2\text{ }:\text{ }3\text{ }\left( {40} \right).\text{ }4\text{ }+\text{ }2\text{ }+\text{ }3\text{ }=\text{ }9.[/latex]
[latex]\scriptsize \displaystyle 4[/latex] of the [latex]\scriptsize \displaystyle 9[/latex] units are nitrogen and [latex]\scriptsize \displaystyle 12\text{ g}[/latex] of nitrogen is needed, therefore:
[latex]\scriptsize \displaystyle \displaystyle \frac{4}{9}\times[/latex]total mass of nutrients required = [latex]\scriptsize \displaystyle 12\text{ g}.[/latex]
Total mass of nutrients required = [latex]\scriptsize \displaystyle 12\text{ g }\times \displaystyle \frac{9}{4}\text{ }=\text{ }27\text{ g}[/latex]
[latex]\scriptsize \displaystyle 40\%[/latex] of the sample contains nutrients, therefore:
[latex]\scriptsize \displaystyle 40\%[/latex] of fertiliser required = [latex]\scriptsize \displaystyle 27\text{ g}[/latex]
Total fertiliser required = [latex]\scriptsize \displaystyle \frac{{27}}{{0.40}}=67.5\text{ g}[/latex] - .
- [latex]\scriptsize \displaystyle {{\text{N}}_{{\text{2}\left( \text{g} \right)}}}\text{+3}{{\text{H}}_{{\text{2}\left( \text{g} \right)}}}\rightleftharpoons 2\text{N}{{\text{H}}_{{\text{3}\left( \text{g} \right)}}}[/latex]
- When the temperature of any reaction is increased, the rate of both the forward and the reverse reactions will be increased. However, the forward reaction is exothermic. Raising the temperature would favour the reaction which would remove the excess heat. The reverse reaction will therefore be favoured more than the forward reaction. This will result in more [latex]\scriptsize \displaystyle \text{N}{{\text{H}}_{\text{3}}}[/latex] decomposing to form [latex]\scriptsize \displaystyle {{\text{H}}_{\text{2}}}[/latex] and[latex]\scriptsize \displaystyle {{\text{N}}_{\text{2}}}[/latex]. The overall result will be that more reactants will be formed.
- Raising the pressure will shift the equilibrium to decrease the pressure. This would favour the reaction which produced fewer gas molecules. The forward reaction produces [latex]\scriptsize \displaystyle ~2[/latex] moles of gas (compared to the [latex]\scriptsize 4[/latex] moles of the reverse reaction). The forward reaction will therefore be favoured. The overall result will be that more products will be formed.
- .
- Water and dilute [latex]\scriptsize \displaystyle \text{NaOH}[/latex]
- chlorine gas
- This type of cell has an ion permeable membrane that allows the positive [latex]\scriptsize \displaystyle \text{N}{{\text{a}}^{\text{+}}}[/latex] ions to move from the anode compartment to the cathode compartment and interact with the [latex]\scriptsize \displaystyle \text{O}{{\text{H}}^{\text{-}}}[/latex] ions.
- [latex]\scriptsize \displaystyle \text{N}{{\text{a}}^{\text{+}}}_{{\left( {\text{aq}} \right)}}\text{+O}{{\text{H}}^{\text{-}}}_{{\left( {\text{aq}} \right)}}\to \text{NaO}{{\text{H}}_{{\left( {\text{aq}} \right)}}}[/latex]
- .
- chloride ions ([latex]\scriptsize \displaystyle \text{C}{{\text{l}}^{\text{-}}}[/latex]) and sodium ions ([latex]\scriptsize \displaystyle \text{N}{{\text{a}}^{\text{+}}}[/latex])
- [latex]\scriptsize \displaystyle \text{2C}{{\text{l}}^{\text{-}}}_{{\left( {\text{aq}} \right)}}\text{+ 2}{{\text{e}}^{\text{-}}}\to \text{C}{{\text{l}}_{{\text{2}\left( \text{g} \right)}}}[/latex]
- [latex]\scriptsize \displaystyle \text{2}{{\text{H}}_{\text{2}}}{{\text{O}}_{{\left( \text{l} \right)}}}\text{+2}{{\text{e}}^{\text{-}}}\to {{\text{H}}_{{\text{2}\left( \text{g} \right)}}}\text{+2O}{{\text{H}}^{\text{-}}}_{{\left( {\text{aq}} \right)}}[/latex]
- sodium ions
- [latex]\scriptsize \displaystyle \text{C}{{\text{l}}_{{\text{2}\left( \text{g} \right)}}}\text{+}{{\text{H}}_{\text{2}}}{{\text{O}}_{{\left( \text{l} \right)}}}\to \text{HOC}{{\text{l}}_{{\left( {\text{aq}} \right)}}}\text{+HC}{{\text{l}}_{{\left( {\text{aq}} \right)}}}[/latex]
Media Attributions
- Fig 1 © MSU is licensed under a All Rights Reserved license
- Fig 2 (2) © DHET is licensed under a CC BY (Attribution) license
- Fig 3 © Von Sasol is licensed under a CC BY-SA (Attribution ShareAlike) license
- Fig 4 © DHET is licensed under a CC BY (Attribution) license
- Fig 5 © Statista is licensed under a CC BY-NC (Attribution NonCommercial) license
- Fig 6 © Siyavula is licensed under a CC BY-NC (Attribution NonCommercial) license
- Fig 7 © Statista is licensed under a CC BY-NC (Attribution NonCommercial) license
- Fig 8 © Siyavula is licensed under a CC BY-NC (Attribution NonCommercial) license
- Fig 9 © LinguisticDemographer is licensed under a Public Domain license
- Fig 10 © DHET is licensed under a CC BY (Attribution) license
- Fig 11 © DHET is licensed under a CC BY (Attribution) license
- Fig 12 © Siyavula is licensed under a CC BY-NC (Attribution NonCommercial) license
- Fig 13 © Libretext is licensed under a Public Domain license
- Fig 14 © https://intl.siyavula.com/read/science/grade-12/electrochemical-reactions/13-electrochemical-reactions-07 is licensed under a CC BY-NC (Attribution NonCommercial) license
- Fig 15 © Siyavula is licensed under a CC BY-NC (Attribution NonCommercial) license
- Fig 16 © Siyavula is licensed under a CC BY-NC (Attribution NonCommercial) license
- Fig 17 © Siyavula is licensed under a CC BY-NC (Attribution NonCommercial) license
- Fig 18